Home » Articles posted by Tessa Sanderson (Page 13)
Author Archives: Tessa Sanderson
Florida’s Roads, Bridges Beat National Score on Infrastructure Report Card
Florida’s roads and bridges rated above the national score on its 2021 Report Card issued by the American Society of Civil Engineers.
The state’s bridges were rated a “B” and its roads a C-plus.
In comparison, nationally, bridges rated a “C” and roads rated a “D.”
“Only 31% of Florida’s major roadways are in poor condition, compared to 42% nationally,” ASCE says.
The organization points out that the state saw a 2.7 million increase in population over the last decade. It attributes the grades to the Florida Department of Transportation maintaining existing infrastructure before starting projects to increase traffic capacity.
ASCE also notes that about 65% of the state’s bridges are in good condition. Comparatively, 45% of bridges nationally are rated good.
Only 3% of Florida’s bridges are in poor condition; whereas, 7% nationally are rated poor.
The state’s gas tax is indexed to inflation, and state funding also continues to increase for transportation infrastructure, contributing to road and bridge conditions, ASCE says.
Though the state has a high rate of bridges deemed good, that number has dropped in recent years, and its number of poor bridges has risen, according to ASCE.
Overall grade
Florida’s overall infrastructure grade also tops the national mark, scoring a “C.”
The national grade is a C-minus.
Though higher than the national average, a “C” is still considered “mediocre” on the ASCE report card. An “A” is exceptional; a “B” is good; “D” is poor; “F” is failing.
Here’s a breakdown of the other categories other than roads and bridges in the scoring:
Aviation (C+) – Tourism and air cargo continue to grow, stressing the state’s airports. But major airports are investing in capacity expansion projects. Ports (B) – The state pumped over $1 billion into its seaports between 2011 and 2018.Dams (D-) – This is Florida’s weakest spot in the report. Only 41% of dams have an emergency action plan compared with 81% nationally.Levees (D+) Energy (C+) – Utilities are burying thousands of miles of lines and investing in weatherproofing the power grid. Solid waste (B+) – The state recycles 43% of its municipal solid waste, compared to the national average of 24%. It also converts a large amount of that waste to energy.Drinking water (C)Stormwater (C-)Wastewater (C)Coastal areas (C-)Schools (D+)Transit (C)
To view the state’s full report, click here.
Did you miss our previous article…
https://constructionosa.org/?p=671
Check Out These 4 Rugged Construction Phones, Including the New Cat S22 Flip
The ruggedized phone has seen a resurgence of product releases this year, and this time a seemingly retro product – yesterday’s flip phone – is getting a new look. We’ll first look at the newest offering in this category and then review the other ruggedized phones that have made headlines this year.
Cat…with a flip
Cat S22 Flip phoneBullitt GroupThe siren call of smart phones has frustrated many construction supervisors observing crew members on their phones instead of working. One possible answer: ban smart phones and require a flip phone.
There are a couple of options out there, including the just-released $234 Cat S22 Flip, an Android 11 Go phone that runs on T- Mobil’s 4G LTE network.
“It really simplifies what a phone should be,” says Adrianne O’Hare, senior manager, brand marketing for Bullitt Group, the Cat phone licensee. “It has all the same rugged features and credentials that you would expect from any Cat phone.”
The S22 is simplicity and functionality wrapped up in an exterior designed to take on construction. Drop proof, dust proof and waterproof, the S22 offers voice and text, fast internet browsing and access to essential apps. Users have access to email, camera, social media, maps, search, talk-to-text and Google Assistant.
“There are a lot more businesses that are looking to go into a low-cost device that’s easy to use and offers fewer distractions,” O’Hare says. “Android Go is like a hybrid version between what’s available on a traditional flip phone and a smart phone.”
The essentials of the familiar flip design are still there: no calls when closed, so no need to worry about accidental dials. When closed, the front window gives you at-a-glance date, time and battery life. The S22 also has a large glove-friendly keypad, a dedicated programmable side button for push-to-talk capabilities and amped up volume that gives you the ability to hear in noisy environments. The 2,000-mAh removable battery lasts and “an entire day and beyond,” Bullitt says.
The phone meets toughness standards, including IP68 ingress protection and MIL SPEC 810H certification. Waterproof to 5 feet for 35 minutes, it has also survived repeated drop testing from 6 feet onto steel on every side and corner, and the hinge has been tested 150,000 times, Bullitt says. The 2.8-inch internal touch screen is protected by Corning Gorilla Glass 5 and optimized for use with wet-finger or glove-on working technology.
“The large keys were important since those in the field are always wearing gloves,” O’Hare says. “You don’t have to worry about taking off your gloves or if you’re in a wet environment.” The S22 can also be used in potentially hazardous work environments and is certified to be non-incendive, Class 1, Division 2, Group A-D, 4T.
Although the Cat S22 is available only on T-Mobile at present, Bullitt says it is in discussions with other partners.
RUGGED PHONES ALSO INTRODUCED THIS YEAR
Sonim XP3plus
Another rugged flip phone offering is Sonim Technologies’ XPSplus, built on the company’s predecessor XP3 model. Advantages over the previous model includes a larger display, additional programmable buttons and an intuitive user interface with dynamic soft keys.
The unit also has a larger battery that offers 15 hours of talk and 440 hours of standby.
The XPSplus is compatible with a range of industrial-grade accessories, including headsets, remote speaker microphones and vehicle mounts. It has an 8-megapixel front camera; non-camera models are available.
Drop proof and waterproof, the XP3plus withstands falls onto concrete from about 5 feet and can be submerged for 30 minutes in 4.9 feet of water. It operates in temperatures ranging from -4 degrees to 131 degrees Fahrenheit.
Cat S62 Pro, Cat S62
Cat S62 ProBullitt GroupCat licensee Bullitt Group also introduced two smart phones this year, the full-on spec-heavy Cat S62 Pro, introduced in April, and the sleeker Cat S62, introduced in June.
The Cat S62 Pro came with a nice surprise: priced at $649 it was significantly lower than its $899 predecessor S61, introduced in 2018. It features a high-definition FLIR Lepton 3.5 thermal imaging camera, helping users locate and diagnose damp areas, leaks, hot spots, electrical shorts, blockages or elevated temperatures.
This thermal imagery can also be blended with images from the phones 12MP dual pixel Sony camera or used with FLIR’s variable intensity multi-spectral dynamic imaging technology, which overlays linear detail from a scene onto the thermal image.
Cat S62Bullitt GroupThe military-grade Cat S62 doesn’t have the FLIR camera but does offer both heft and sleekness. Bullitt says the phone doesn’t have the rubber overmolding or raised edges of the S62 Pro but “it’s got the same rocket engine.”
Its 4,000-mAh battery can last for up to two days before needing a charge. The phone, priced at $498, includes a fingerprint sensor for security, login and remote payments.
Did you miss our previous article…
https://constructionosa.org/?p=665
Inside the Ritchie/SmartEquip Deal: What Happens Next?
When Ritchie Bros. Auctioneers acquired SmartEquip for $175 million in September, Ritchie CEO Ann Fandozzi said it would give Ritchie “asset-specific full-lifecycle parts and service support” to dealers, OEM partners and equipment buyers.
Of equal importance as SmartEquip considered suitors was continuating its multi-brand approach in the construction industry, says Alex Schuessler, SmartEquip founder and president, international group, talking with Equipment World.
SchuesslerSmartEquip”There was a lot of interest from other industries and private equity firms, but what really drew us to this partnership with Ritchie was a continued commitment to our existing customer base,” Schuessler says. “It was important for us to preserve industry neutrality. It took us a long time for our customers to feel comfortable that we were truly neutral, so that was absolutely critical going forward.”
In turn, SmartEquip, which provides software to support equipment lifecycle management, gives Ritchie a play on the parts, service and maintenance side of things, says Jim Kessler, president and COO, Ritchie.
“We knew how long it would take us to do this on our own and replicate what SmartEquip has already built,” Kessler says. “So for us it was the perfect match. We had customers who need this service and we weren’t able to provide it; it was an open hole for us. We know what the equipment is. We know where it is in the life cycle, how many hours on it, but we weren’t helping in that part of the value chain.”
But Kessler also emphasizes that the SmartEquip deal doesn’t mean it is in the parts stocking business. Rather, Ritchie is looking to add customer ease and value, he says.
“The magic in all of this is the equipment life cycle, and Ritchie has done phenomenal work in focusing not just on the moments that equipment changes ownership, but also what you do to support the equipment owners, dealers and manufacturers,” Schuessler says.
Hidden owners
This especially comes into play with second and third owners of a machine where perhaps dealers and OEMs lose track of them. “We were looking at ways of ensuring that they have a longer view across the equipment life cycle and across the number of owners,” Schuessler says.
“We’ve long been aware that there are tremendous opportunities there with that second, third or fourth owner,” Schuessler says, “and it’s been frustrating because we’ve had no systematic way of supporting them. I think we’ll be able to help both equipment owners and dealers right off the bat.”
The trust built between SmartEquip and its dealer and OEM customers has been hard fought, Schuessler says. The firm began in 2000, right on the heels of the dot-com craze when everything was about reducing the number of intermediaries in a transaction.
“That’s not at all what we wanted to do,” Schuessler explains. “We wanted to bring efficiency to the relationships of dealers and OEMs on one hand and the fleet owners on the other.” In the process, SmartEquip gave OEMs and dealers a systematic way to tie in deeper into the life cycle and go into those second and third owners. “Now with Ritchie we can automatically do this together, and we can offer it straightaway,” he says.
For the foreseeable future, SmartEquip will continue to operate as a standalone business headquartered in Norwalk, Connecticut.
Both companies have a global footprint. SmartEquip has been operational in Europe for around 10 years, Schuessler says, and just announced a previous agreement with Tokyo-based Diamond Construction Equipment and that its network was fully operational in Japan. (Diamond Construction is co-owned by four large Japanese equipment rental companies and Mitsubishi.) Ritchie’s purchase of SmartEquip allows it to “be so much more responsive with our international business,” Schuessler says.
Supply chain perspectives
You can’t have a discussion with supply chain front row players such as Ritchie and SmartEquip without delving into the issues that are plaguing all industries these days. Schuessler sees two issues: components and whole goods.
“In Japan, rental fleets tend to hold on to their equipment two to three times longer than they would in North America or Europe,” Schuessler says. “Of course, as equipment gets older, parts consumption goes up, as do service needs. That means two things. For those fleets that tend to have a longer life, the value we can bring to them by making those parts efficient also goes up over time relative to other parts of the world. If you take a step back to look at the overall life cycle, the contribution that technology brings to the lifecycle costs in an aging fleet tends to be higher than it is when you only hang on to it for two to four years.
“On the parts side, the shortage means that the search cost is higher, and so much of what SmartEquip does is reduce the search costs. When we began as a company, it was not unusual for a technician to spend as much time looking for the right part from a preferred supplier as they would holding a wrench in their hands. While we can’t change the scarcity aspect of it, we do have the ability to find the parts out there that pertain to a particular serial number.”
In this tight supply market, Ritchie is focused on how it can add value, Kessler says. “We’re also working on our technology to make sure that when you are ready to transact in the future it’s easy to do,” he says. For example, Ritchie’s Inventory Management System “makes it easy to transact with us,” he says. “There are other value-added things that our customers would appreciate.”
“We’re very happy to have them on board,” Kessler says. “We don’t have a rush to try to force something, so we want to make sure we build a technology that’s going to be easy for everyone to use. This isn’t about Ritchie trying to change it and make it something that it’s not. We want to make sure that when the marketplace is ready that it’s easy to use, and everyone’s going to have full transparency of how it’s going to work for them.”
Schuessler says the real benefit will come when today’s “spot technologies” telematics, fleet management, etc. are knitted together. “There’s no new technology required; it’s all about the workflow now,” he says. “If a machine throws out a code, we should be able to order a part and have it waiting at the service bay with a work order already filled out and technician instructions on what needs to happen. Raising the efficiency is right there to be had.”
2021 Contractor of the Year: Pruss Excavation Refashions Fleet After Meeting Dual Flood Challenges
The construction lineage is deep in the Pruss family. Matt’s grandfather, Jim Sr., started Pruss Excavation in 1968. His father, also named Jim, joined him four years later, and Matt came on board in 2001.
But Matt’s start in construction goes much further back than 2001.
“I got on an excavator when I was 10 years old. When my dad told me to dig, I just kept on digging,” he says with a laugh. “Mom freaked out, but I enjoyed it.” And as he was growing up, both he and brother Scott, who now serves as superintendent with Pruss Excavation, pitched in when his father found himself shorthanded.
Matt went on to get a construction management degree, something he didn’t know was available until Freshman Day at the University of Nebraska. He had planned to go into business, but after the dean of the university’s construction management college learned his dad was a contractor, he convinced Matt to switch majors.
“We had some amazing professors who gave us real-world scenarios,” Matt says.
One example: it’s bid day and the students are estimating a project. The professor would go through the students with a handful of papers with vendor and sub quotes. “He would literally just throw them your way,” Matt recalls. “Some quotes didn’t have bonding and some didn’t include taxes, and you had figure out the good ones to develop the bid.”
Matt thought the exercise was exaggerated until he got back into the family business right after college. “It was not,” he says.
When Matt came on board, his father’s first instinct was to put him behind the controls of a machine, because he knew exactly how much operator/machine hours translated to the bottom line.
Matt had other ideas, though. Working in what then were company offices – in the basement of his parents’ home – he started estimating and soon bidding jobs that were outside of the company’s typical work of building terraces for area farmers.
“I know Pruss Excavation grew because of my education,” he now says. “We could get into the commercial side and chase bigger work.”
So the company began to expand, eventually moving from the basement office to a separate structure on the family farm in Dodge, Nebraska, one and a half hours northwest of Omaha.
Now Pruss Excavation logs $7 million to $10 million in annual revenues, has around 40 employees and does a variety of work, including dams and levees, roadwork grading, wetlands, landfill cell construction, site work and lagoons.
The transition from father to son was gradual as Matt took on bidding, contract management and submittals. And his brother Scott Pruss now manages several in-field duties, including serving as the firm’s quality control manager.
A turning point was a $3.4 million dam project in 2008; the company came in low by $13,000.
“It was a great job for us,” Matt recalls. Started right before the economy soured in the Great Recession, it also helped the company weather that economic storm.
Floodwaters
Pruss Excavation was to weather more storms, this time the meteorological variety. Major floods hit Nebraska in 2011 and 2019, and both changed the makeup of the company’s equipment fleet.
During the 2011 flood, Cat dealer NMC called and asked Matt if he still had the Challenger tractors with pull-behind scrapers. The company had eight at the time.
NMC was renting haul trucks to the U.S. Army Corps of Engineers on levee repair work after the flood, and the Corps decided the trucks weren’t the right equipment for the job. It was spending too much time building roads for the trucks and not enough time hauling dirt.
Pruss soon had six Challengers with pull-behind scrapers on the job and then bought five more from a dealer in Florida. Even that wasn’t enough, and it had to rent additional machines.
“By the time that project was done, we had 70 machines running, including 23 pull-behinds along with support equipment,” Matt says. “That was our huge, giant boost. Before, we were doing around $3 million a year, and with that project, we hit more than $8 million.”
It didn’t hurt that the job had a $43-an-hour federal wage. “I had guys from all over the country wanting to work for us,” Matt says. “Finding labor was not an issue.”
Of course, high demand comes with its own challenges. Pruss’s competition was doing the same thing, and everyone was scrambling for equipment and parts.
The 2011 and 2019 Nebraska floods helped Pruss Excavation up its equipment fleet and project management skills.Pruss ExcavationThe 2019 flood also had an equipment fleet impact, with Pruss buying six dozers to handle the flood mitigation work. “We were going in with 40 additional people, so I was buying things up like crazy,” he says. “We had nine dozers on that site running every day.” The job also racked up machine hours. “At one time we were working 12-hour days seven days a week. My operators were making amazing money.”
Pruss also put two mechanics on the 18-month job. “I knew stuff was going to fail and what we had to do to fix it,” he says.
In assessing the levee repairs done on the project, a reviewer with the U.S. Army Corps of Engineers ranked Pruss’s quality and scheduling as “exceptional.” The review said: “Not only was the levee repair a phenomenal effort and of exceptional quality, but the Pruss Excavation team even went out of their way to ensure that all work areas were clean and properly grade.”
The Corps took special note of how the two Pruss brothers worked together: “Matt and Scott’s combined teamwork really and truly enabled the success of this project…[they] were always synchronized in all efforts and activities and any absence by one was seamless with no disruption in performance.”
Regarding cost control, the Corps assessment added: “It was a skillful performance, and Matt’s pricing and responsiveness rivals that of much larger organizations observed over the past two years performing similar work. The best aspect of working with them is that they always construct a great product.”
Of course, the all-of-the-sudden levee repair work had to be managed with prior commitments.
“They had a very challenging project with us, and they continued to push through on our job and honor their obligations even while they were doing the levee work,” says Luke Ridder with Hawkins Construction.
Pruss Excavation jobsite huddle.“A lot of contractors would just chase the flood work,” he adds, “but Matt stuck around, and he kept the job moving. It was a big deal. Matt knows he can’t just be an owner and pick up a paycheck. He’s very involved and he drives the ship on their modeling.”
This flood remediation experience came into play when the company bid on an emergency $1.05 million contract with a 144-hour turnaround. The job required over 33,500 tons of materials to be imported to close a breach that was 350 feet long and over 25 fee deep with flood water still flowing through it. “We had a pre-bid meeting at 1 p.m., they wanted bids at 4 p.m. and would sign the contract at 4:05 p.m.,” Matt says. “We were low by $11,800 and got it done early.” The project required a dozen operators and 30 trucks.
“A week later we were low bid on another fast-track levee repair,” Matt says. “We were low by $55,000 on a $2.8 million contract with a 168- hour completion. We successfully completed that repair on-time as well.”
Matching fleet to job demand
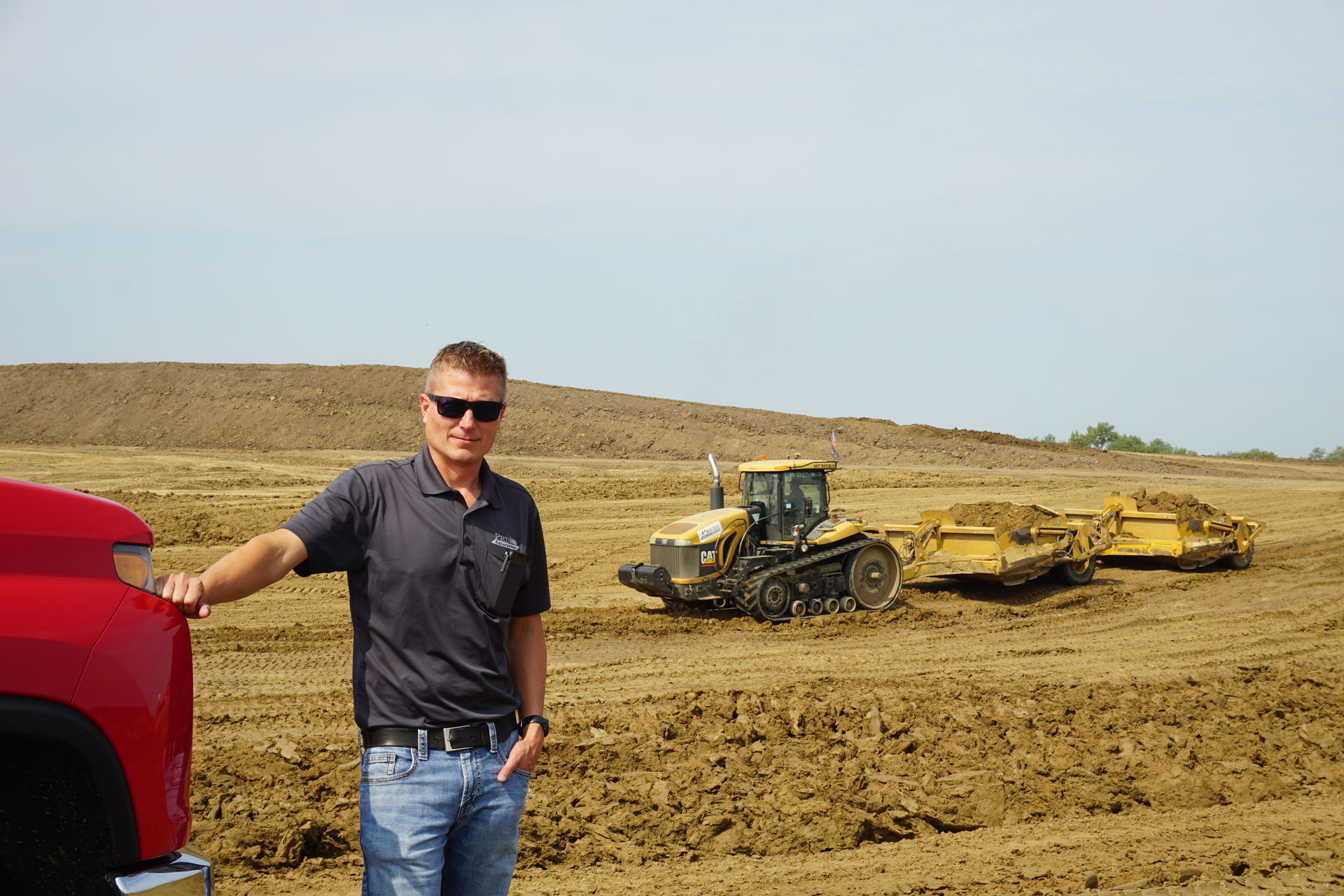
The company’s fleet of pull-behind scrapers — now at 32 — has helped them tackle wet conditions.
“We have had more machines than people throughout the years, and we’re still that way,” Matt says. This also allows Pruss Excavation to stage an upcoming jobsite while finishing another and thus lessen time spent on mobilization.
Its fleet of pull-behind scrapers now numbers 32. “Pull-types are awesome in the wet and the sand,” Matt says, noting that the company also uses Cat 627 self-propelled scrapers in drier conditions.
Although the bulk of his fleet is in the large machine category – including dozers, excavators, articulated trucks, scrapers and scraper tractors – Matt also uses skid steers as support machines. “We’re also heavy into Topcon GPS,” he says, “and in addition to dozers, scrapers, and motor graders, we also put the excavators on grade control. We’ve found it very user friendly.”
While operators are responsible for daily greasing, Pruss uses NMC to handle PM tasks. “They’ll service my entire fleet, no matter the brand,” he says. Engine, transmission and other major repairs go to dealers.
Today’s machine telematics also help with service, he says. “When we get a warning, dealers can diagnose and know where the machine is and what they need to fix it.”
But he’s also learned these convenient diagnostics can eat up tech time if an easy fix is not readily apparent. “I always press my dealers for warranties that cover diagnostics,” Matt says. “I don’t want to be billed for the time it takes them to figure out a problem.”
Legacy
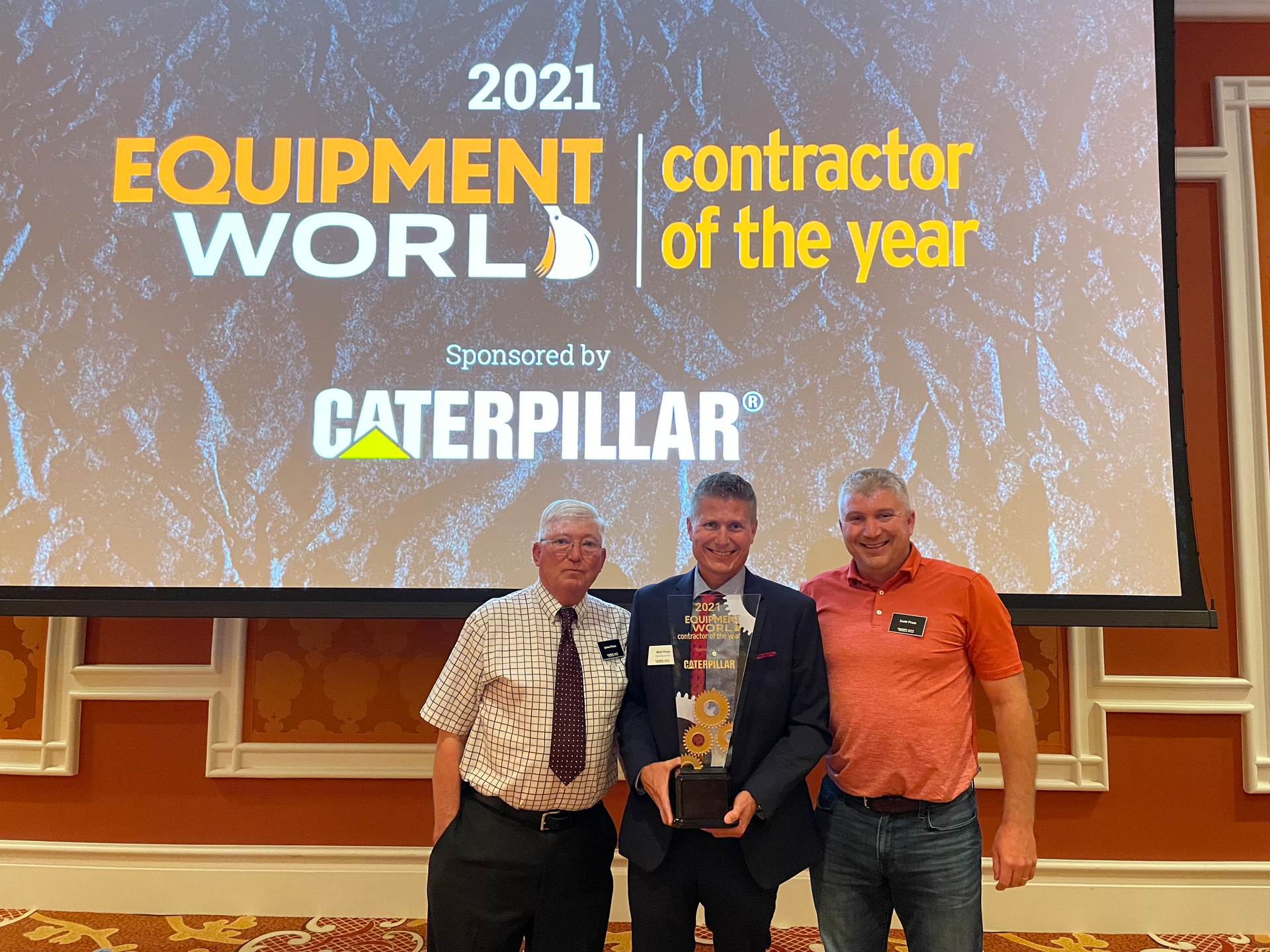
Father Jim Pruss (left) and brother Scott Pruss (right) flank Matt Pruss at the Contractor of the Year event.
Being named the 2021 Contractor of the Year has special resonance for Matt: His father, Jim Pruss Jr., was named a Contractor of the Year finalist in 2004. Both his father and brother attended the Contractor of the Year event last month and witnessed his win.
Neither is surprised he came away with the award. Matt’s clients and vendors also notice his attention to detail in how he approaches his jobs.
“He’s a heck of a businessman,” says his dealer representative Kevin Peterson with NMC. “And you can see it in the way he’s grown.”
“They know the type of leadership it takes to run a great small business,” says Ridder. “They just get it done.”
“We let our work to speak for us,” Matt says. “We want to under-promise and over perform instead of the other way around.”
Watch Matt Pruss receive the Contractor of the Year award below:
Product Roundup: JLG expanding its aerial lift product line
JLG to add rotary telehandlers
JLG announced that it is partnering with Italian manufacturer Dieci to bring a new line of rotary telehandlers models to market. The JLG rotating telehandler line will initially consist of three models, the R1370, R1385 and R11100 with max lift heights from 67.3 to 97.1 feet and max lift capacities of 11,000 to 13,200 pounds.
Long popular in Europe, the rotating design works well on narrow city streets or anywhere space is constrained. This feature also enables you to get more work with less repositioning of the machine. The new line of JLG rotary telehandlers will be available with 13 attachments at launch for added versatility.
With more than 70% of a machine’s weight composed of steel, Volvo and SSAB intend to reduce the carbon used in its manufacture.Volvo Construction Equipment
Volvo CE’s first fossil-free steel vehicle
Volvo has been pushing the envelope for a decade or more when it comes to environmental improvements to its equipment and operations. Its latest innovation is the first vehicle made with fossil-free steel in Volvo Construction Equipment’s factory in Braås, Sweden.
The concept vehicle, unveiled October 13 in Gothenburg, Sweden, is a load carrier for mining and quarry work. According to Melker Jernberg, president of Volvo CE, the company intends to have fossil-free steel used in all its products. Volvo says more vehicles with fossil-free steel are coming in 2022, including a series of concept vehicles and components.
The steel for the concept vehicle was provided by SSAB, headquartered in Stockholm, with facilities in Finland and the United States. You may recognize one of SSAB’s more well-known products here: Hardox wear plate and Strenx performance steels for dump trucks and other high-abrasion applications.
Crowded streets and confined jobsites are no problem for Liebherr’s new MK 73-3.1 crane.Liebherr
“You want that drywall where?” Liebherr’s new crane easily lifts over the gnarliest obstacles
The new MK 73-3.1 crane from Liebherr offers compact dimensions, making it a good choice for projects in densely built areas or where you need to perform multiple lifts to different points on a jobsite without having to reposition. According to the company, setup can be accomplished in as little as 10 minutes.
The smallest of Liebherr’s mobile construction cranes, the MK 73-3.1 measures 45 feet (13.8 meters) long, 8.8 feet (2.7 meters) wide and 13 feet (4 meters) in height, but it also includes all the features of its bigger brother the MK 88-4.1. The new crane can be operated electrically on site or powered by its integrated drive unit. The electric mode is quiet and emissions free, which is desirable in urban environments. A single Cummins six-cylinder diesel engine provides both drive and lifting power. Smart assistance systems and an adjustable elevating cabin support the lifting and positioning of heavy loads.
Max lifting capacity for the MK 73-3.1 is 13,225 pounds (6,000 kg), and 4,400 pounds (2,000 kg) at full radius. The top hook height is 87 feet (26.5 meters) high. Slewing radius is 11 feet (3.5 meters). The crane weighs 36 tons and can take on 2.9 tons of additional ballast for heavier lifts.
The Terramac RT7U can be customized to meet customers’ needs.Terramac
Customize your crawler carrier from Terramac
Shown at The Utility Expo, the Terramac RT7U is purpose-built for utility applications and capable of accommodating a wide array of support equipment.
The carrier’s rubber tracks and low ground pressure enable crews to access remote locations with difficult terrain.
Terex Washing Systems
Easily transport Terex’s new mobile washing screen
Terex Washing Systems launched the M1700X mobile washing screen at Ireland’s Construction & Quarry Machinery Show.
The screen can produce up to five products (three aggregates and two sands), the company says. The M1700X is easily transported, has a short 15-minute setup time and has optional hybrid power.
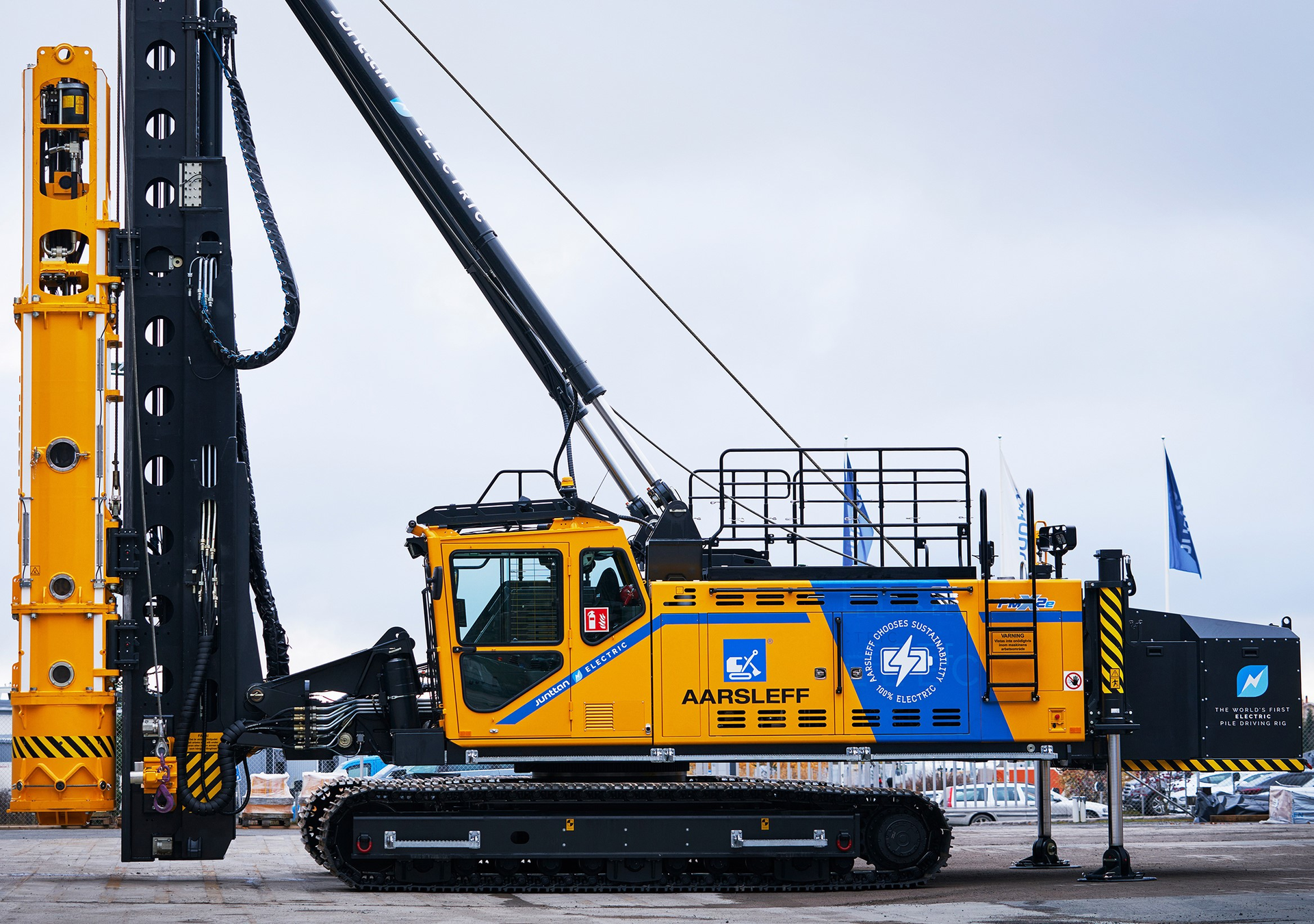
Junttan’s introduction of the world’s first electric pile driving rig will support Aarsleff’s mission to reduce the carbon dioxide emissions that originate from fossil fuels.Junttan
Junttan launches world’s first electric pile-driving rig>
Junttan Oy and Per Aarsleff A/S have formed an alliance to bring the world’s first battery-powered electric pile-driving rig to market.
The PMx2e is modeled after the diesel-powered PMx22. The electric pile-driving rig will offer the same “robust structure and usability as the PMx22 but consumes less energy per pile, reduces noise and delivers more power and instant torque,” Junttan says.
The rig features two detachable 396 kWh battery packs to allow for 8 to 13 hours of continuous pile driving. The battery packs replace the counterweight on the machine and can be charged with a normal 63A mains outlet.
Aarsleff Ground Engineering AB is a Swedish subsidiary of the Danish construction company Per Aarsleff A/S and is one of Sweden’s leading companies in ground engineering. The goal between the manufacturer and end user is to create more environmentally friendly construction sites through the reduction of carbon dioxide emissions that originate from fossil fuels.
Junttan Also Signs Dealer Agreement with XCMG for Foundation Drilling Rigs
Junttan USA Inc., a subsidiary of Junttan Oy, will represent XCMG foundation drilling rigs in the United States.
The rigs, custom-built by XCMG for Junttan, will be backed by a full line of drilling tools, temporary casings, shoes, drive adapters and teeth. The XCMG line of drilling rigs has a range of operating weights from 45 to 200 tons and torque values between 130 and 800 kNm. >
The partnership will expand Junttan’s product line from primarily pile-driving equipment into foundation drilling equipment.>
Electric Pickup Trucks to Watch in the Next 3 Years
Competition in the electric pickup truck market is getting fierce. With several new models recently announced and others slated for delivery in early 2022, drivers will soon be able to put them to the test.
There’s no doubt that electric vehicles have the necessary speed and torque. But battery life, towing capacity and charging infrastructure…that’s a different story.
While electric cars have caught on quickly, the average truck buyer is going to require more arm twisting. If you’re thinking of greening up your fleet in the coming years, here are all the electric pickup truck models to keep an eye on.
Atlis Motor Vehicles
Atlis XT
Atlis Motor Vehicles says its XT electric work truck can be recharged in just 15 minutes and offers 500 miles of range.
The XT pickup has a 10,000-pound tow rating and can be fitted with a 6.5-foot bed, 8-foot bed, flatbed or service body.
The startup company plans to begin production in late 2022 with prices starting at $45,000.
Bollinger
Bollinger B2
Watch your wallet! The boxy and industrial Bollinger B2 comes with a hefty price tag of $125,000. The Michigan-based startup, which has pushed back production dates multiple times, says delivery will start in 2022.
With an estimated range of 200 miles, the B2 falls short compared to some of its competitors. Bollinger says the Class 3 truck is built for off-roading and will feature a 7,500-pound towing capacity and a 5,000-pound payload capacity.
Chevrolet
Chevrolet Silverado Electric Pickup
GM will debut the all-electric Chevrolet Silverado on January 5 at the Consumer Electronics Show.
Powered by GM’s Ultium Platform, the manufacturer will build the battery pack into the vehicle’s frame.
The truck will feature a segment-leading fixed glass roof for increased visibility and headroom. This is the first application of a fixed glass roof on a GM pickup.
Four-wheel steering will allow for improved turning radius, handling and stability.
On a full charge, GM estimates the electric Silverado has a range of more than 400 miles. No word yet on the price.
Ford
Ford F-150 Lightning
With more than 120,000 customer reservations, interest is high for the all-electric version of America’s best-selling truck. One factor may be the F-150 Lightning’s modest price tag. The truck starts at $39,974.
The F-150 Lightning delivers 563 horsepower and 775 pound-feet of torque. It supports a 2,000-pound payload on the standard model and 10,000 pounds of towing capacity on XLT and Lariat models with the extended-range battery and Max Trailer Tow Package.
Ford says the truck’s battery can also serve as a backup power system for your home or charge tools and devices on the jobsite.
GMC
GMC Hummer EV SUT
GMC’s Hummer is coming back from the dead, but this time as an all-electric pickup truck. (The more familiar SUV model will be available at a later date.)
The pickup will feature a three-motor, four-wheel-drive system with 11,500 pound-feet of torque. Drivers can expect a range of 350 miles when fully charged. It will make use of the same Ultium battery platform as the electric Chevrolet Silverado.
Starting at $112,595, the Hummer EV Edition 1 is pricey. Cheaper models will be available by early 2024.
Lordstown Motors
Lordstown Motors Endurance
The Endurance is the first commercial vehicle to feature four in-wheel hub motors. Lordstown Motors says this design reduces the number of moving parts and improves vehicle control.
Priced at $52,500, the Endurance will have an estimated range of 250 miles and a towing capacity of 6,000 pounds.
Deliveries are slated for the first quarter of 2022, but recent turnover in company leadership has left some skeptical.
Ram
Ram 1500 EV
Ram fans, sit tight. The company won’t be releasing its all-electric half-ton pickup until 2024.
With a driving range of 500 miles and towing capacity of more than 10,000 pounds, Ram says the truck will outperform its competitors.
The starting price has not been released but will likely be competitive with other major manufacturers in the same size class.
RJ Scaringe @RJScaringe Twitter
Rivian R1T
Rivian staked its claim as the first manufacturer in the U.S. to bring a mass-produced, all-electric pickup to market. The Class 2b truck with a dinky 4.5-foot bed will likely be a better fit for families and outdoor enthusiasts than construction business owners though.
The base battery offers a 300-mile-plus estimated range, but a 400-mile-plus battery can be purchased for an additional $10,000.
The R1T uses a four-motor, all-wheel-drive system and has a towing capacity of 11,000 pounds.
The truck starts at $67,000. The first customer vehicle rolled off the production line in September.
Tesla Cybertruck
Tesla Cybertruck
Slated for production in late 2022, the Tesla Cybertruck has totally reimagined the look of the pickup truck.
The stainless-steel truck will feature all-wheel drive, 14,000 pounds of towing capacity (in the three-motor model), and an estimated range of 500-plus miles. An air suspension system can raise and lower the truck on the fly offering 16 inches of ground clearance.
The Cybertruck starts at $39,900, and buyers can add on Tesla’s full self-driving option for an additional $7,000.
Toyota also plans on electrifying its pickups, but no word yet on a model or launch date.
Which major manufacturer or startup will be the leader of the pack? Only time will tell.
Did you miss our previous article…
https://constructionosa.org/?p=612
The Future of Paving? Volvo Unveils Its CX01 Concept Compactor
Asphalt compactors aren’t known as the most difficult machine to operate on the job. Although compactors perform a critical function especially when smoothness specs are at stake, many contractors put their less-seasoned operators on them.
But what if these machines didn’t even require an on-board operator?
Enter Volvo Construction Equipment’s CX01 asphalt compaction concept, a planned ConExpo reveal that had to wait until the recent Utility Expo to get in front of contractors.
“We just wanted to examine what the future of compaction would look like,” Justin Zupanc, head of Volvo CE’s asphalt compaction development team, told Equipment World at the show. “We wanted to create a better operator’s environment, reduce fuel consumption and exhaust emissions and boost productivity.”
“Better operator environment” translates to no cab. Instead, a connected fleet of CX01 single-drum units directed by a downloaded compaction plan would be either be remotely controlled by an operator or controlled autonomously.
Volvo already has an autonomous system on its TA15 haulers, now in customer testing, and the plan is to test a similar system on the CX01, Zupanc says.
The CX01 does not have an articulation joint “so there’s no balance point, there’s nothing that we can steer away from,” Zupanc says. Volvo solved this by using a split-drum which has two halves that can be operated independently kept upright by using a self-balancing control system. (The split drum comes off of its current 9-ton class machine sold in Europe.) To turn, operators can vary the rate of speed of each half of the drum. “You can make a fairly tight turn,” he says.
And while it wouldn’t be used while the unit is on asphalt, users also would have the ability to pivot steer the machine.
Rethink the paving process
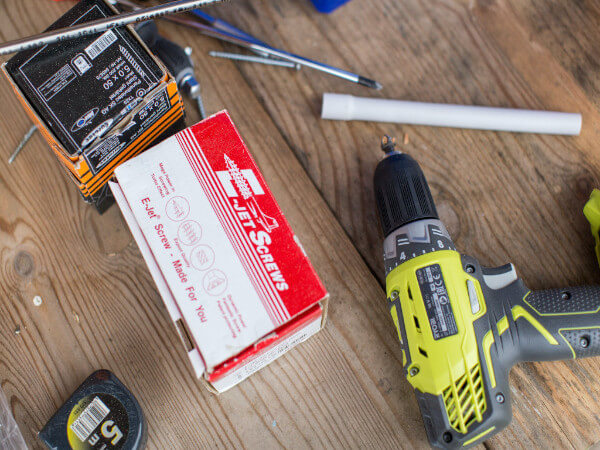
The Volvo CX01 prototype compactor features guarding and emergency stops on each corner.Equipment World
Volvo says the CX01 which stands for compaction experimental unit No. 1 provides the means to “fundamentally rethink the paving process.” By removing the operator, you’re also removing their exposure to vibration, noise and dust.
As envisioned, a fleet of CX01s could be deployed on larger jobs and communicate not only with each other but with other machines on site. The machines could survey the job, report on mat conditions such as density, temperature and passes (which intelligent compactors are already doing) and determine when and where to compact. “They can shift over if an area is already compacted,” Zupanc says. “All information is available to the crew and to other machines. You could even send it to the asphalt plant.”
The machine’s compact design and maneuverability could also lead to streamlined compaction cycles, reduced costs and more agile work patterns, Volvo says. The rolling pattern, weight and number of rollers could be adjusted to match the width, thickness and speed of the paving operation. Using Volvo’s existing Co-Pilot system, operators can use a touchscreen to remotely control the compactors.
Flexible power
The CX01 has a flexible power system. It has both a 1.7-liter diesel engine and an energy storage system that can be operated indiesel-only, hybrid or fully electric modes. “The diesel is only there to spin the 20-kilowatt generator,” Zupanc says. The generator in turn powers two 48-volt ultracapacitors placed on each side of the drum, which in turn are powering three 14-kilowatt electric motors, one for each side of the drum, and another to power the vibration system eccentrics.
“You can run it with the diesel engine on, and it’s always charging the ultracapacitors,” Zupanc says. When the ultracapacitors are charged, the engine can be turned off, and the machine becomes fully electric. The engine will cycle back on when the ultracapacitor charges get low. “They charge very quickly, within a couple of minutes,” he says. The downside: the capacitors don’t have the capacity of a lithium-ion battery; runtime is around 20 minutes, depending on your speed.
“We had never used them before, and we wanted to see how they worked,” Zupanc says, explaining why Volvo was using ultracapacitors on the CX01. “While they don’t have the capacity of lithium-ion batteries, they are good for vibration and they have a long lifecycle. They may not be the right solution because they don’t have that longevity, and who knows, we may couple them with a lithium-ion battery pack down the road.”
Because the ultracapacitors need a constant charge, it’s unlikely that the diesel engine will go away as long as they are used.
Volvo is also exploring using a low-friction water-reduction polymer-based coating on the drum surface now theoretical — which could also be used on its other compactors. This would combat the common problem of asphalt sticking to the drum, now solved by using water. The CX01, however, has limited water storage.
Volvo produced =the following explainer video of how it envisions the CX01 being used:
RIICO Recruitment 2021 for Various Posts | 217 Posts | 13-11- 2021
RIICO Recruitment 2021 for Various Posts with 217 Posts vacancies, last date to apply is 13-11- 2021, apply now
The post RIICO Recruitment 2021 for Various Posts | 217 Posts | 13-11- 2021 appeared first on ConstructionPlacements.
Did you miss our previous article…
https://constructionosa.org/?p=582
Top Auto Accessories that Make a Construction Project Easier
Any true builder knows that being able to successfully complete a construction project is no simple task. There are a whole host of confounding factors that can slow or halt the completion of a project if not handled properly. However, one aspect of the work that you can control is having the right gear. Whether you’re a project manager, general contractor, or at home-handyman, having the right tools and accessories for the job is critical to success. Outfitting your work vehicle with accessories suited to construction is one way you can make your next project much less of a headache. Here are some of the top auto accessories that will help you simplify your next project.
The post Top Auto Accessories that Make a Construction Project Easier appeared first on ConstructionPlacements.
Did you miss our previous article…
https://constructionosa.org/?p=579
Lay Aggregate, Streamline Backfilling with Road Widener FH-R
The Road Widener FH-R material placement attachment, showcased at The Utility Expo, enables one crew member to precisely lay topsoil, gravel, asphalt and more.
The remote-controlled attachment can be connected to skid steers, compact track loaders, road graders and wheel loaders. It is designed for such tasks as road shoulder repairs, remediation, road widening and trench backfilling.
Because the attachment operates off the host machine’s engine and hydraulics, there is no engine or transmission to maintain. Road Widener says this can reduce maintenance costs by 90% compared to self-propelled machines. Customers have also reported a 50 percent savings in labor costs thanks to the remote control.
“The FH-R cuts out jobsite clutter and enhances efficiency by eliminating extra machines and reducing the multi-step process down to just two passes, dispensing and compacting,” said Lynn Marsh, Road Widener president. “Contractors will get a high-quality, profitable and efficient solution for their business that makes for an unrivaled total cost of ownership.”
The FH-R is available in left, right or dual dispensing configurations. Operators can choose from dispensing widths ranging from 1 to 6 feet. The attachment can dispense up to 20 tons of material in under 10 minutes without the need for additional scraping or sweeping, the company says. A 360-degree swivel caster allows the attachment to easily maneuver around posts, guard rails or other common objects.
The FH-R works with standard and high-flow hydraulics and has only five grease fittings to maintain. It is available with an optional universal mounting plate to ensure smooth compatibility and connection.
The attachment fits on the same commercial trailer as the host machine and can be towed by a pickup truck.
Did you miss our previous article…
https://constructionosa.org/?p=576