Home » Articles posted by Tessa Sanderson (Page 17)
Author Archives: Tessa Sanderson
12 Road Projects Named Finalists for America’s Transportation Awards
After months of regional competitions, 12 road construction projects have been chosen as finalists for America’s Transportation Awards.
The awards, sponsored by the American Association of State Highway and Transportation Officials, include projects in Arizona, Delaware, Florida, Indiana, Kansas, Kentucky, New Jersey, North Carolina, Oregon, Pennsylvania, South Carolina and Utah. Along with AASHTO, the U.S. Chamber of Commerce and AAA sponsor the awards program.
“This competition recognizes just a few examples that highlight the ways in which state DOTs are improving quality of life and economic vitality of our communities, saving time and money through new innovations and technologies, and making better use of assets already in place,” says Jim Tymon, AASHTO executive director.
The grand prize and People’s Choice winners will be announced October 26. Each winner receives $10,000 cash to donate to the charity of its choice. The competition evaluates projects in three categories: Quality of Life/Community Development; Best Use of Technology & Innovation; and Operations Excellence.
Finalists are also categorized by project size: small (projects costing up to $25 million); medium (projects costing between $26 million to $200 million); and large (projects costing more than $200 million).
Here are the 12 finalists:
Kentucky Transportation Cabinet – Brent Spence Bridge Emergency Repair Project (Operations Excellence, Small project group) (Photo above.)
Safety for drivers, cyclists and pedestrians was improved with the $13.9 million widening of the Fourth Street Bridge over Interstate 40 in Flagstaff, Arizona.Arizona Department of TransportationArizona DOT – Fourth Street Bridge over Interstate 40 (Quality of Life/Community Development, Medium project group)
The Delaware Department of Transportation alleviated traffic congestion and created more transportation options for a Wilmington community by constructing the $82 million Senator Margaret Rose Henry Bridge.Delaware DOTDelaware DOT – Margaret Rose Henry Bridge and Approach Roads (Operations Excellence, Medium project group)
The Florida DOT deployed a SMART Work Zone System that included a temporary traffic signal, three closed circuit cameras and nine Bluetooth devices on its project to improve the Cow Key Bridge.Florida Department of TransportationFlorida DOT – Leveraging Innovation: How FDOT Transformed the Gateway to Florida Keys (Best Use of Technology & Innovation, Small project group)
The Indiana Department of Transportation opened the Grand Valley Boulevard Bridge on June 15, 2020, in Martinsville. Replacing a section of four-lane State Road 37, the bridge gives drivers and pedestrians a safe connection to neighborhoods, schools and businesses.Indiana Department of TransportationIndiana DOT – Grand Valley Boulevard Bridge (Quality of Life/Community Development, Small project group)
Originally designed as a toll road in the 1960s but toll booths were never installed, the Turner Diagonal Interchange in Kansas City had three miles of obsolete and hazardous ramps. The Kansas Department of Transportation’s $30.3 million project increased safety and economic development.Kansas DOTKansas DOT – Turner Diagonal: Partnering for Growth (Operations Excellence, Medium project group)
The $25 million Route 1 Permanent Hard Shoulder Running Project overseen by the New Jersey Department of Transportation improved safety, increased emergency access, increased capacity and travel reliability, and cut commute times by up to 50 percent.New Jersey DOTNew Jersey DOT – Route 1 Permanent Hard Shoulder Running Project (Operations Excellence, Small project group)
The $101.6 million Salem Parkway improvement project in Winston-Salem, North Carolina. The project included 10 bridge replacements, two new pedestrian bridges, a walking and biking path and extended sidewalks.NCDOTNorth Carolina DOT – Reconstruction of Salem Parkway (U.S. 421/I-40 Business) (Quality of Life/Community Development, Medium project group)
Oregon Department of Transportation developed a $15.6 million automated system that posts real-time weather, traffic flow and surface condition readings on digital billboards on Interstate 84 in northeastern Oregon.Oregon DOTOregon DOT – I-84 Snow Zone Safety Improvement Project (Operations Excellence, Small project group)
To improve accessibility and safety for motorists, bicyclists, boaters and pedestrians along SR 381, the Pennsylvania Department of Transportation launched a $12.8 million multimodal gateway project at Ohiopyle State Park.PennDOTPennsylvania DOT – Ohiopyle Multimodal Gateway (Quality of Life/Community Development, Small project group)
This stretch of scenic S.C. 61 in the Charleston area underwent a $4.4 million improvement project to add new lanes and widen shoulders while reducing the number of trees cut.SCDOTSouth Carolina DOT – C. 61 Phase 1 (Rural Road Safety Program) (Operations Excellence, Small project group)
The Utah Department of Transportation completed a $415 million project that widened I-15 to six lanes in each direction, reconfigured two interchanges, replaced 15 bridges, built a new bridge, and created a new flyover ramp to address traffic congestion in rapidly growing Lehi.Utah Department of TransportationUtah DOT – I-15; Lehi Main to S.R. 92, Technology Corridor (Quality of Life/Community Development, Large project group)
An independent panel of transportation experts will choose the Grand Prize winner, while the public will select the People’s Choice Award winner through online voting weighted to each state’s population, AASHTO says.
The online voting ends at 11:59 p.m. October 25. Votes can be cast at AmericasTransportationAwards.org.
AASHTO will announce the winners during its Annual Meeting October 26-29 in San Diego.
Did you miss our previous article…
https://constructionosa.org/?p=399
Women in Construction: Planning Your Post-Pandemic Career Path
If you’re a woman working in the post-pandemic world, construction isn’t a bad place to be. While there is still a wage gap between men and women, it’s less than in other industries, with women earning 99.1% of what their male counterparts make.
The pandemic hasn’t slowed things down, either. A survey of 700 women in construction in March found that 58% said they’re working about the same compared with before the pandemic, while nearly one-third (32%) said they’re working more, and only 1 in 10 reported working fewer hours. Meanwhile, 71% said opportunities are on the increase, while 28% said they were about the same, leaving just 1% to report they were declining.
This leaves women in construction with a leg up on women in other fields, such as retail and hospitality, who have been struggling to retain their jobs during the pandemic. Instead of scrambling to get back to where they were pre-COVID, many women in construction are riding the crest of a wave.
Opportunities Abound
Restaurant, retail, and travel industry closures hit women in those industries hard. Employment in February was down by 383,000 jobs compared with the year-earlier total in retail alone. Leisure and hospitality employment job losses were even worse, at 3.9 million.
Although many jobs in the latter sector are opening back up as travel and tourism increase, many displaced workers will see a chance to shift gears and find opportunities await in construction, where a March estimate identified a need for 200,000 skilled craft professionals. And these positions pay well, upwards of $66,000 for a carpenter, for example. To compare, a general contractor can make an average salary of $70,000 to $95,000 a year.
There’s room for growth, too: Women make up just 10.3% of the construction workforce, which means there’s both a challenge and an opportunity.
Stereotypes Persist
Many women may not even consider construction because of stereotypes that have kept trade industries male-dominated for some time. Media representations from Bob the Builder to Wreck it Ralph to Tim Allen’s Home Improvement are geared toward male audiences.
Women, meanwhile, have been dismissed as no longer “needed” in construction jobs.This is similar to what happened after World War II ended, with “homemaker” conventions resurfacing to replace Rosie the Riveter.
It’s still assumed by many that construction is a male industry. But that’s simply a false assumption, and it’s limiting both women and the companies that could be benefiting from their talents.
Challenging those stereotypes will be important moving forward in order to take advantage of opportunities that are opening up. A more diverse workforce increases the labor pool. It also boosts productivity and provides a greater variety of perspectives to promote innovation and better decision-making.
Technologies & Trends Emerge
From drones and artificial intelligence to 3D printing and modeling, construction technology is becoming more relevant by the day. As the industry as a whole embraces data as a driving factor in decision-making, it is becoming more obvious that the soft skills women bring to the table as effective communicators and team players improve both productivity and safety. That means, for women in tech, the emphasis on working smarter could help them get their foot in the proverbial door.
Similarly, emerging trends in construction will expand opportunities for women in tech to break into adjacent industries. For example, new directives designed to address the climate crisis have resulted in an industry-wide push to achieve net-zero energy in both new construction and retrofitting. As a result, subcontractors in heating, plumbing, electrical, and alternative energy (to name a few) will be looking for sustainability experts to help them “go green” and stay relevant.
Entrepreneurship is Rewarded
Self-employed construction workers are a force to be reckoned with. More than 23% of U.S. construction workers were self-employed in 2018, compared to 10% of the broader workforce.
As of 2016, more than one-third of carpenters (33.6%) were self-employed, nearly 42% of floor layers were, along with 38% of construction managers and 41.3% of construction and maintenance painters.
That means there’s plenty of opportunity to be your own boss under the right conditions. Of course, that takes understanding things like the need for various kinds of insurance, such as workers’ compensation (if you have employees), property and liability, and general liability.
It also means having enough capital and credit to make a go of it. If you’re thinking of going into business yourself, now is the time to get your finances in order so you’ll be in a position to invest in yourself and your company. As an added bonus, taking steps to build your credit can save you up to $11,460 per year in interest rates and fees on loans and credit cards.
## Alternatives are Available
If you have taken time off from your career, either due to the pandemic or personal reasons, you have options. Returnships encourage professionals who’ve taken a break from the workforce to get back in the game.
These paid internships allow companies and potential employees to get a feel for each other and provide training that can help in the long run, whether you wind up with that particular company or not. Companies like CDM Smith and Caterpillar are among those that offer or have offered returnships, often with a focus on women.
Opportunities in construction will continue to expand, but as stereotypes persist, it’s important for women to remain confident in what they have to offer, because it’s significant. Women can provide a broader and more diverse pool of labor and ideas that will serve the construction industry well in the years to come.
Schedule a Demo
Jessica Larson is a married Midwestern mom and a solopreneur. She creates online courses for students, and has started and run several other businesses through the years. Her goals are to support her family while still actually spending time with them, to act as an entrepreneurial role model for her two daughters, and to share what she has learned through The Solopreneur Journal.
Did you miss our previous article…
https://constructionosa.org/?p=387
Deere: Split With Hitachi Allows It to Flex Technology Muscle
What was behind the surprising Deere-Hitachi excavator split announced in August? What will this mean for Deere customers of both brands?
P
RuccoloJohn Deereerhaps a better question is what it won’t mean, says Domenic Ruccolo, speaking to Equipment World about the split. Ruccolo, a Deere veteran, is the company’s new senior vice president of sales, marketing and product support, global construction equipment. He also serves as chief sales officer for the Wirtgen Group.
“From a customer-support standpoint, I think the best way to put it is that there will be no change,” Ruccolo says. Irrespective of brand, Deere dealers will continue to support everything they have sold over the years “indefinitely,” he says.
“There’s no question that we had a very successful partnership with Hitachi throughout the Americas for more than 30 years,” Ruccolo says. But times have changed, and “it was the right time for both of us to make this change,” he says. “Where we are really going our separate ways is on the marketing and product support side.”
After Feb. 28th, Hitachi Construction Machinery Americas will take over distribution and sale of its excavators. Hitachi plans to manufacture all of its excavators in Japan and import them to the North and South American markets. All manufacturing plants in the joint venture will remain with Deere post-split. This includes its flagship manufacturing facility in Kernersville, North Carolina, as well as plants in Brazil and British Columbia.
That doesn’t mean all has ended between the two companies, however. “We’re going to continue to have a strong relationship with Hitachi for years to come through our continuing supply agreement with them,” Ruccolo says.
Hitachi plants in Japan, for instance, will still make its above 47-metric-ton models, the 670G and 870G, and its 190G wheeled excavator.
Technology centric
During the joint venture, Deere relied on Hitachi’s excavator technology, although Ruccolo points out that Deere has developed its own excavator models over the past 13 years that were sold in markets such as Australia, Southeast Asia and Russia. “The agreement gives us the flexibility to transition on a model-by-model basis to Deere technology,” Ruccolo says. “We’re really excited about the opportunity to control our own journey in excavators.”
Ruccolo also says this transition to Deere technology supports the company’s overall smart industrial strategy announced in 2020.
“Obviously when we have our own technology in excavators, it makes the deployment of them a lot easier for us,” he says. Deere can also apply technologies to excavators that it develops in other markets — notably agriculture and as the result of acquisitions such as autonomous driving start-up Bear Flag Robotics.
Dealer reaction
Ruccolo says the Hitachi split was not expected by dealers, “and there was a bit of a shock factor.”
Still, “there’s a lot of excitement and a lot of energy around what the future holds” on the dealer side, he says. “Once we had the opportunity to explain the transition and what the future holds I think generally dealers are quite excited about the future.”
He also says that by now Deere dealers are already well-versed in Deere’s new smart investment strategy. “Customers are going to experience the same continuity and exceptional support that comes in the form of reliable access to parts, solutions and service,” he says.
Three years down the road?
If plans proceed as envisioned, three years from now contractors will look back on an uninterrupted customer experience, Ruccolo says. “We intend to be there every step of the way from a support standpoint for our customers and dealers,” he comments.
And will the Kernersville plant start to produce excavators beyond its current 13- to 47-metric-ton segment? Ruccolo declined to comment.
The Deere-designed and manufactured excavator line, however, will be in full transition. “We want to accelerate the development of what we feel is industry-leading technology and machinery,” he says. “We’re full steam ahead.”
Did you miss our previous article…
https://constructionosa.org/?p=381
Ways to Boost Productivity in Your Construction Business
The efficiency of a construction site depends on the productivity of the workforce, sufficient planning, and proper site management. Meeting the demands of the growing construction industry calls for innovative solutions to improve productivity.
Overview
The construction industry continues to flourish as a growing population and urbanization fuels the demand for infrastructure, residential and non-residential properties. Despite representing 13% of the global GDP (gross domestic product), the sector experiences slow productivity growth. Over the past two decades, productivity has grown at an annual rate of one percent. Due to the low productivity, the sector experiences project delays that lead to budgeting complexities and the disruption of workflows.
Some of the productivity challenges in the construction industry are:
* Slow implementation of technology and automation tools
* Poor communication and coordination among the workforce
* Inefficient utilization of time
* Skilled labor shortage
For the sector to enhance its efficiency, it is crucial for stakeholders to seek solutions that address technological, workforce, and fleet management gaps. Apart from streamlining operations, these solutions guarantee a smooth transition towards sustainability in the construction sector.
In general, workforce productivity in the construction sector estimates the physical progress per unit per person-hour or any other metrics adopted by a company. For companies to sufficiently quantify productivity, they have to measure:
* The level of effectiveness of the labor — What is the total cost for constructing a unit area?
* Relative efficiency of the workforce — Is the workforce performing the right tasks at the right time?
Improving the productivity of the construction workforce comes with radical changes in sector regulations, research and design practices, workforce management, and on-site management strategies. Construction companies can boost their productivity by incorporating the following ideas into their business operations.
1. Implement digital technology
The project design phase consumes a considerable amount of time. Most businesses create standard design libraries for repeatable construction elements to reduce project design time. Through digital tools such as BIM (building information modeling), companies can create multiple designs, develop digital prototypes, and analyze the sustainability of new construction materials before physical implementation.
Using the 5-D BIM technology grants an organization the ability to transition into complex projects like underwater civil projects which adopt non-conventional parameter specifications.
At construction sites, supervisors work with extensive teams. They assign work and dispatch employees to the appropriate working locations depending on their skills and availability. While performing their duties, the company has to update the attendance of the workforce in real-time, keep a log of construction activities, and reconcile payrolls to match timesheets.
Relying on manual tools to perform these tasks is tedious and can impede the transparency of operations. Through technology, companies can improve workforce management by providing automated tools for multi-location scheduling and timesheet management. It creates transparency and allows the company to track productivity in real-time, facilitates accurate dispensation of information, and enhances labor planning to avert employee shortages.
Reducing construction waste, site safety incidents, and supply chain inconsistencies remains a challenge in the construction sector, leading to project delays. Companies are undertaking rigorous research and development to optimize operations and minimize risk, which causes costly delays. Technologies like digital twins enable companies to optimize their designs, while analytics software provides them with insights on how to streamline supply chains. In the process, the company minimizes project execution costs and effectively utilizes the workforce.
2. Continuously train your workforce
Although the construction sector is enjoying steady growth, it is facing a shortage of skilled workers. As a result, companies have to find anyone interested in the construction work and expose them to on-the-job training. For business owners, they have to offer reasonable financial compensation to their skilled workforce. Apart from prioritizing cost-effective operations, companies have to maintain a stable workforce.
Companies that establish apprenticeship programs can attract a younger talent pool. Such programs ensure that the skills of the workforce meet the prevailing business needs. The apprentices learn the ropes of a trade by engaging in different construction tasks, equipping them with all-around skills. In due course, the team of apprentices fills in the vacant positions or replaces the aging workforce, ensuring the continuity of business operations.
As technological solutions make their way into the construction sector, there is a need for business owners to equip their staff with basic IT knowledge. The company hosts these solutions through cloud technologies and distributes them to the workforce through mobile devices or computers. Through training, the company describes how to fill in attendance records, record daily tasks, request materials/tools, and communicate with other team members through mobile applications.
Training is essential for enforcing a safety culture and enables the company to communicate any changes in safety standards. By training the workforce on safety and how to use advanced technological tools, companies enhance productivity by:
* Minimizing safety incidents
* Ensuring the workforce performs the correct work at the right time
* Providing timely access to critical information on mobile devices on project changes
3. Streamline on-site implementation
Streamlining on-site implementation involves a raft of lean operational measures that:
* Limit redundant activities
* Eliminate downtime
* Maximize construction materials — Keep construction waste at manageable levels
* Increase the utilization of construction equipment — Availability and timely maintenance of equipment
* Prevent unnecessary downtime — Non-designated break from work
To successfully streamline site operations, companies need to combine technology and encourage a progressive mindset among the workforce. They have to understand the importance of completing tasks within the desired timelines. The company should establish and enforce safety and construction standards, monitor the discipline of the workforce, and retain efficient workflows.
By assigning KPIs (key performance indicators), business owners can evaluate the project progress and organize rewards or incentives for teams that complete milestones in time. It motivates the workforce and encourages them to meet project goals.
Planning plays a crucial role in the success of any project. Before beginning the project, the company needs to create a PID (project initiation document) which lays down all the project requirements, project costs, and implementation timelines. It enables the company to plan for the workforce, formulate project goals, and create site-specific productivity measurement metrics.
The company needs to create a solid plan for logistics and supply chains. It minimizes interruptions to construction schedules and averts resource misallocation or misappropriation. With proper planning, every team member becomes aware of the project’s workflow process and productivity enhancement measures.
4. Keep communication clear
Solving productivity problems requires proper communication between the different levels of the workforce. Every team member, beginning from the architects to the on-site construction employee has to read from the same page at every project stage. Senior-level management must be aware of any on-site constraints and challenges affecting site construction workers. On the other hand, the implementation teams require timely updates on policy changes and project variations.
Slight communication breakdowns can result in project variations which is a leading cause for rework. When companies establish clear communication channels like Fieldwire, it is easier for employees from different professions to coordinate. Through mutual coordination, they can identify process bottlenecks and brainstorm ideas to eliminate them. With the evolving technology, the company distributes newsletters, reviews, and informational articles through mobile-based applications.
When companies communicate the importance of productivity to their employees and how it impacts daily schedules, the workforce develops a workplace culture that fosters teamwork, respect for each other, and adherence to site protocols. Communication channels serve as avenues for supervisors to conduct remote check-ins and verify whether the employees are at their designated places of work. It simplifies employee management and improves employee morale.
Summing Up
As the construction industry adjusts to market dynamics, business owners need to work towards improving the productivity of their workforce. Companies need to update their operating standards, match the skills demands of the employees, and adopt technological solutions as much as possible. Investing in the relevant technology guarantees workforce visibility and supplements project management strategies to steer businesses towards better profitability.
To understand how Fieldwire can help you and your team manage people and projects more efficiently, please register for a live demo of our platform below.
Schedule Demo
Derek spearheads key initiatives at Deputy, a global workforce management platform for employee scheduling, timesheets and communication. With a focus on construction and healthcare, Derek helps business owners and workforce leaders simplify employment law compliance, keep labor cost in line and build award-winning workplaces. Derek has over 16 years’ experience in delivering data-driven sales and marketing strategies to SaaS companies like MarketSource and Griswold Home Care.
Did you miss our previous article…
https://constructionosa.org/?p=375
Industry Roundup: H & E relocates Little Rock branch
H & E Equipment Services has relocated its Little Rock branch, renovating a 6,450-square foot facility in Mabelvale, Arkansas. The facility includes a fully fenced yard, offices, parts warehouse and a repair shop with six service bays.
“To best serve customer demand, we recently sold our Komatsu dealership rights in Arkansas along with our former Little Rock property to focus specifically on rentals, the largest growth area of our business,” says Trent Taylor, branch manager. “Our plan is to aggressively grow our rental fleet and expand our product offering of quality equipment with competitive rates throughout the central Arkansas area.”
The Little Rock branch specializes in the rental of aerial lifts, telescopic forklifts, earthmoving machinery, compaction equipment, generators, compressors and more.
Hyundai adds Delta Power Equipment
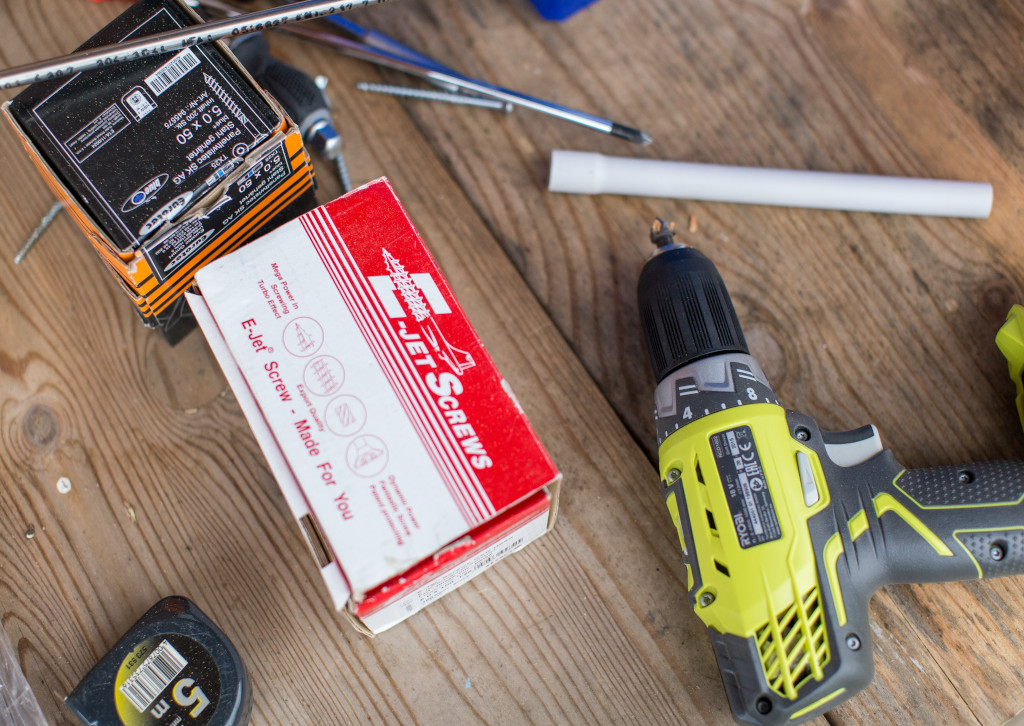
Left to Right: Cameron Currie, general sales manager and Brad Blain, construction sales manager, Delta Power Equipment.Hyundai Construction Equipment Americas
Hyundai Construction Equipment Americas has added Delta Power Equipment to its North American dealer network. Delta serves agricultural, construction and power sports markets in multiple locations across Ontario. Hyundai equipment will be available at the company’s Essex, Forest, Mitchell, Sparta, Waterford and Winchester locations.
ProSource Machinery named Hydrema dealer
ProSource Machinery will now offer Hydrema articulated dump trucks. The company will represent Hydrema throughout Colorado from its Platteville location.
Chadwick-BaRoss buys J. F. McDermott
Chadwick-BaRoss has completed acquisition of waste-and waste-water-industries supplier J. F. McDermott. Chadwick-BaRoss now has nine locations in New England.
MANUFACTURERS, SUPPLIERS
Yanmar announces new president, executives
JohnsonYanmarYanmar Compact Equipment and ASV Holdings brands have named Tate Johnson president, Lee Thole director of aftermarket and David Gannon as director of channel development.
Johnson joined the company as commercial director last year, overseeing sales, national accounts, channel development and marketing. As president, he will further develop growth initiatives for the company as the two brands progress in a joint vision of Yanmar Compact Equipment North America.
“As we continue to grow, we will seek to provide even more resources and support to our dealers and in turn, the end user customers,” says Johnson. “The addition of Lee and David is the logical next step.”
Thole’s responsibilities as aftermarket director will include strengthening post-sales support functions and aftermarket strategy. Gannon will work closely with the company’s dealer network, working to recruit new dealers and assist current dealers.
Ritchie reaches $500 million mark with Marketplace-E
Ritchie Bros. says its Marketplace-E price-controlled option has seen sales of more than $500 million in the past 12 months.
The option includes “Buy Now” and “Make Offer” features. Ritchie says it’s driving buyers to the site through real-time demand data. As a result, items “are selling approximately 40% faster on Marketplace-E,” says Kari Taylor, chief revenue officer. Ritchie says more than 2,500 customers used the service to sell items, including Sunbelt Rentals.
“We now have access to an expanded footprint and tools to help us better manage how, when, where, and what price to sell our assets—because we have the flexibility of choosing the proper Richie Bros channels, using a Ritchie Bros. location, or remarketing directly by Sunbelt we are improving the efficiency of our disposition process as well as recovery on equipment sold,” says James Dennis, vice president of fleet management at Sunbelt.
Sheppard joins Machinery Advisors
Luke Sheppard of Sheppard & Company Consulting has joined the Machinery Advisors Consortium. George Russell, MAC co-founder, says Sheppard “will complement the other MAC Advisors with his experience in construction and forestry equipment, his leadership insights revealed in his first book, and his demonstrated results driving success in the key parts and service departments of a large CE dealership.”
Equipment confidence index drops in September
The Equipment Leasing & Finance Foundation’s monthly confidence index dropped from 66.6 in August to 60.5 in September. The index is a qualitative assessment of prevailing business conditions and future expectations as reported by key executives in the equipment finance sector.
When asked to assess their business conditions over the next four months, 17.9% of executives responding said they believe business conditions will improve over the next four months, down from 35.7% in August. Another 71.4% believe business conditions will remain the same over the next four months, up from 64.3% the previous month; 10.7% believe business conditions will worsen, up from none in August.
Executive respondents cited several factors leading to increased uncertainty, including the Delta Covid-19 variant and the inability to fulfill demand because of labor shortages and supply chain shortages.
Woods Equipment names dealer channel director
Woods Equipment has named Darwin “Dag” Parsell to its newly created director of dealer sales channel position. Parsell, previously regional sales manager, will manage sales activities within the North American Woods Ag and Turf dealer organization.
Magni opens Houston-area office
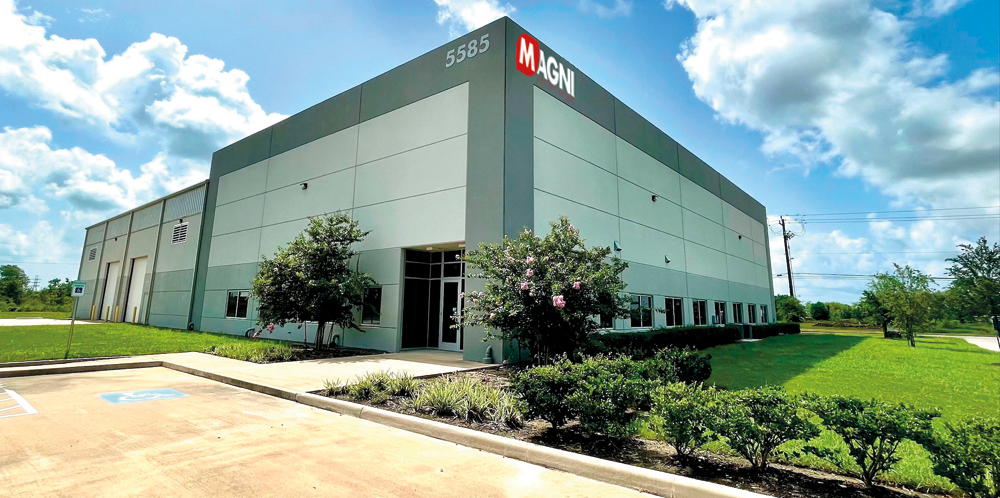
Magni Group says it will use its new facility in Pasadena, Texas, as its main logistics hub for the distribution of spare parts and machines. The facility is in addition to the company’s current U.S. headquarters in New Jersey, which also serves as a parts and machine distribution facility. Magni has also announced plans to start work on a new headquarters in the first quarter of 2022.
Did you miss our previous article…
https://constructionosa.org/?p=332
Used Truck Prices Skyrocket, But Will the Bubble Burst?
The Class 8 auction market heats up more each month, and retail selling prices continue to crush records as the industry stands at the confluence of a strong freight market, an inadequate supply of low- to average-mileage used trucks and a shortage of drivers.
J.D. Power Senior Analyst and Product Manager of Commercial Vehicles Chris Visser, a guest during FTR’s ongoing virtual State of Equipment series, says “superheated rates” are keeping truck buyers energized. FTR forecasts rate increases to gradually relax and reach year-over-year parity starting in early 2022, while volume continues to grow into 2023. “In this market, we’re never going to have enough drivers to move the amount of freight that we have,” he says. “We’re really in a severe shortage of new trucks.”
The four-year truck trade cycle has been alive and well, Visser said, adding that 489,100 orders for trucks have been placed in the last 12 months with a bump in August due to the opening of model year 2023 build slots. However, OEMs have tamped down some of the enthusiasm as uncertainty surrounds the number of trucks they can build due to shortages of various components and workforce challenges.
Based on the number of trucks bought in model years prior, the supply of trades was naturally set to increase by roughly 20% in 2022, but Visser says the new-truck shortage will delay that increase.
Model years 2015 and 2016 are the most common trucks on the auction market, Visser notes, adding that if you can find three- or four-year-old trucks at auction, be ready to pay upwards of $100,000 for them.
“2019s are three years old, and those trucks are selling for well over $100,000 on the retail market,” Visser says, “and they’re being snapped up.”
Year-over-year auction pricing has increased more quickly and steeply than retail, as a lack of inventory is currently limiting sales.
“Dealers would sell more trucks if they had more trucks to sell,” Visser says.
An increasing number of fleets are bypassing dealers and auctions to dispose of late-model trucks because they’re so easy to sell. Visser adds the overall truck shortage has also pushed more fleets to the auction market as buyers, pitting them head-to-head against dealers and wholesalers on the auction floor and further driving up prices.
“When there’s no bargain price equipment that’s unwanted, (trucking) business is tough,” Visser says. “It’s getting more and more difficult for an owner-operator to purchase a used truck.”
Trucks 4 to 6 years old brought 86.5% more money at auction from January to July this year compared to the same period in 2020. Monthly appreciation has averaged roughly 4.8% in 2021.
Retail pricing is now at a post-Great Recession high with monthly appreciation of 3- to 5-year-old trucks averaging 1.8% per month across-the-board and increasing to 5.3% for trucks with fewer than 500,000 miles.
Visser says J.D. Power’s 48-month residual forecasts will likely be adjusted upward due to lower than predicted build rate of model year 2022 and 2023 trucks. While there’s no change in sight for current conditions, he said pricing will eventually pull back.
The used truck market will turn fairly quickly when new truck production returns to normal, parts shortages end and fleets start remarketing more trades through auctions, leaving the number of trucks on the ground and negative equity as concerns when supply returns to trend, Visser said.
“I won’t say the bubble bursts,” he says, “but eventually pricing will return closer to trend as the availability of new trucks increases and economic factors work themselves out of the economy.”
Fuel-saving equipment
Fuel-friendly specs 6x2s, wide-base wheels and aerodynamic equipment are hitting the used market in higher numbers, “and they do take a fairly substantial hit on the used side,” Visser says of used truck buyers typically seeking a dual rear-wheel, 6X4 configuration.
Wheel covers and chassis fairings, Visser says, also “tend to be one more piece of equipment that break and tend to wear out.”
A full set of aluminum wheels, Visser says, is adding upwards of $2,000 over steel.
The market is also warming up to automated manual transmissions (AMTs). Visser said most of the used truck market currently “wants” an AMT, adding that AMTs are now commanding a $2,000 to $3,000 price premium compared to a comparable manual transmission.
Historically, AMTs have been a pricing deduct compared to manuals, but that dynamic only exists currently with buyers seeking an 18-speed manual.
“Value enhancers are engine size and horsepower,” Visser says, adding that buyers still put a premium on 500-plus-horsepower engines. Other possible equipment on used models include:
Electronic Driver Assist Systems The 2018 model was the first year of widespread installation for Advanced Driver Assistance Systems, and while fleets want this technology on new trucks for safety and insurance savings, individual used buyers often need to be educated on how they work and their benefits.
Gliders Gliders are commanding roughly a 20% premium compared to a factory original unit, applies-to-apples, Visser says, because they are in very limited supply and almost none are entering the market. “That will continue to be the case for the foreseeable future,” he says.
Completed glider builds – Glider builds equipped with refurbished engines and transmissions in new truck bodies and chassis became popular among owner-operators and small fleets as an alternative to buying new in the wake of tightening federal emissions regulations that took effect in 2008 and 2011.
But the U.S. Environmental Protection Agency crippled the glider industry with its Phase II emission regulations, sending independent shops that produced most of the kits retreating to repair/replacement when OEMs stopped selling chassis for gliders or selling gliders themselves.
Did you miss our previous article…
https://constructionosa.org/?p=329
OSHA to Ramp Up Heat-Related Enforcement and Inspections
The Biden administration is calling for stepped up enforcement and increased efforts to prevent heat-related illnesses on the job.
As part of that initiative, the U.S. Occupational Safety and Health Administration plans to increase workplace enforcement and inspections, especially on days when the heat index is above 80 degrees.
“On days when a recognized heat temperature can result in increased risks of heat-related illnesses, OSHA will increase enforcement efforts,” the agency says.
OSHA says it will also develop a National Emphasis Program, in which it will place temporary, intense focus on heat inspections. It also plans to develop a workplace heat standard.
Though construction is among the top industries affected by heat, the administration’s plan is broad-based, also including indoor workers, as well as schools and nursing homes. It cites climate change as leading to extreme heat, which “is now the leading weather-related killer in America.”
“Rising temperatures pose an imminent threat to millions of American workers exposed to the elements, to kids in schools without air conditioning, to seniors in nursing homes without cooling resources and particularly to disadvantaged communities,” President Joe Biden said in announcing the initiative.
The U.S. Department of Labor reports that 43 workers died from heat-related illness in 2019 and 2,410 suffered serious injuries and illnesses from heat. The agency notes that heat illnesses are often underreported. With climate change, DOL says, those conditions will worsen.
OSHA has ordered its area directors throughout the country to do the following:
Prioritize inspections of heat-related complaints, referrals and employer-reported illnesses and initiate an onsite investigation where possible.Instruct compliance safety and health officers, during their travels to jobsites, to conduct an intervention or open an inspection when they observe employees performing strenuous work in hot conditions. An intervention involves providing the agency’s heat poster and wallet card, discussing the importance of easy access to cool water, cooling areas and acclimatization.Expand the scope of other inspections to address heat-related hazards where worksite conditions or other evidence indicates these hazards may be present.
OSHA also calls on employers to intervene with its workers in extreme heat by requiring regular breaks for water, rest and shade; training workers on identifying heat-related symptoms and what to do when a worker suspects a heat-related illness; and taking periodic measurements to determine workers’ heat exposure.
In October, OSHA plans to start the rulemaking process to develop a federal heat standard for indoor and outdoor workplaces.
The agency says the forthcoming National Emphasis Program on heat hazard cases will target high-risk industries and focus resources and staff on heat inspections.
“The Department of Labor, the Department of Health and Human Services, the Environmental Protection Agency and other agencies will work together to help ensure that the American people have safe and healthy working conditions, provide cooling assistance to homes and neighborhoods, and coordinate with state and local officials to bolster their resilience and address the impacts of this threat,” Biden said.
Did you miss our previous article…
https://constructionosa.org/?p=326
Secunderabad Cantonment Board recruitment for Asst. Engineer [Civil], Asst. Cantonment Planner | 06 posts | 09-10-2021
Secunderabad Cantonment Board recruitment for Asst. Engineer [Civil], Asst. Cantonment Planner | 06 posts | 09-10-2021
The post Secunderabad Cantonment Board recruitment for Asst. Engineer [Civil], Asst. Cantonment Planner | 06 posts | 09-10-2021 appeared first on ConstructionPlacements.
Did you miss our previous article…
https://constructionosa.org/?p=323
Plagued with Low Battery Life? These Chargers Will Keep Your Devices Ready to Go
Time for a battery check. You rely on your devices especially phones to power your business. But will they last a full day which in contractor terms means way past eight hours?
The good news: There are a slew of good, reliable and affordable charging options out there. But whatever you buy, be sure to look for these basics:
Size and Capacity: A good rule of thumb for power banks says the bigger the battery, the greater its capacity and the more ports it can accommodate. It’s easy to find an inexpensive one that will fit in your pocket and, with 5,000mAh, reload your phone once or twice. It’s also not hard to find something a bit more robust.
Power In. Power Out: When shopping for a charger or power bank, be sure it’s compatible with the device(s) you’ll be using it with. Most will have a USB-A port for reloading the battery and for sending the juice to your device. More and more devices are relying on USB-C ports, as they are also compatible with most fast-charging options.
And, of course, Apple has a port all its own: Lightning. However, with the Apple iPhone 12, charging can be done with a USB-C port.
So, regardless of the charger or battery pack you buy, be sure its ports match up with your device’s cords.
Wireless Charging Is a Real Thing: Newer models of smartphones and other devices may be set up to be charged without having to be plugged in. Wireless charging relies on electromagnetic induction to reload your device. In short, wireless, or Qi, charging works by transmitting power from a coil in a charging unit to a coil in the receiving device. All you do is place your smartphone or other device on the pad of the receiver.
As we said, there are hundreds of charging devices on the market. With even modest study, you can find one at a travel center, truck stop, big-box store or online that fits your device and your budget.
Here’s a few to get you started:
Jackery Explorer

To the untrained or unfamiliar, putting using this portable power station in your pickup might seem like going rabbit hunting with a Howitzer. But it never hurts to be over-prepared.
Weighing in at just a shade less than 4 pounds, the Explorer packs a big charging wallop and also provides the convenience of not having to reload it too often.
It has a 100-watt AC outlet, a USB-C and two USB-A outlets, and a 12-volt car outlet as well.
And at its heart, the Explorer has rechargeable lithium-ion batteries that provide 167 watt-hours of energy storage. That means it’ll recharge the thirstiest of smartphones 16 times.
You can refill those batteries by plugging into a wall socket (about five hours) or your truck’s 12-volt system as you drive, or hook it to an optional solar panel.
The Explorer 160 sells for about $106 on Jackery’s website.
PowerDrive’s Cup Holder Power Inverter
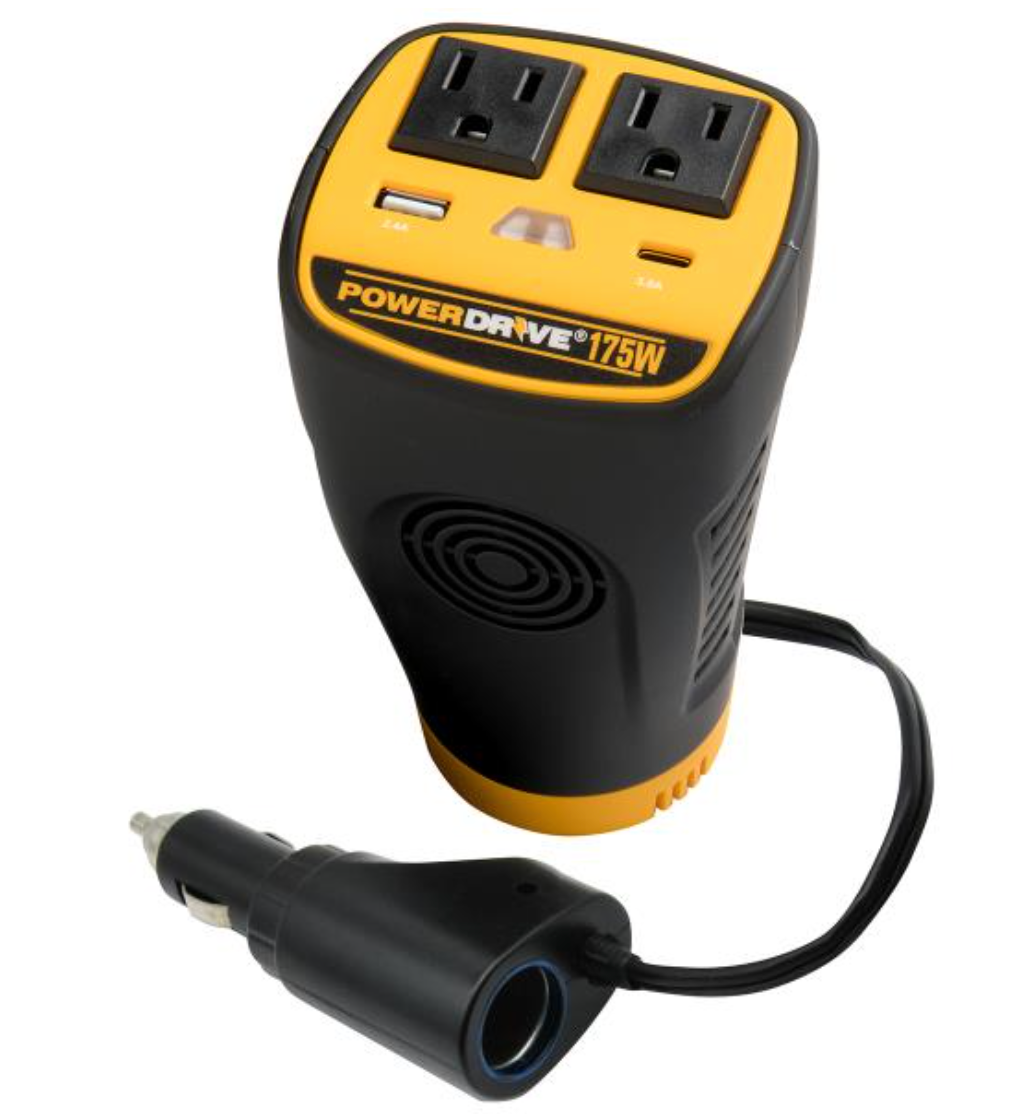
This device not only charges your devices, it also provides AC and 12-volt outlets so you can use your truck’s battery to power other appliances.
Fitting nicely into your truck’s cup holder, it has both USB 2.4 amp and USB-C 3 amp ports, in addition to the AC outlet, making it able to accommodate most of your charging requirements.
It has a 2-foot-long cable to plug into your truck’s 12-volt port.
PowerDrive is a member of the RoadPro Family of Brands, and the cup holder inverter is available at most travel centers and truck stops and sells for $32 online.
Nekteck PD 45W Type-C Car Charger
Don’t be thrown by the name. This’ll work in your truck and delivers plenty of power for a reasonable price – about $20 online.
This device fast-charges phones, tablets and laptops on its USB-C port and, at the same time, can charge a second phone on its USB-A port. It conforms to USB-C fast-charging standards and includes a good quality cable.
This Nekteck’s 45-watt output and its USB-C–to–C cable support the maximum charge rate on Android phones, the 2018 and 2020 iPad Pros, and some laptops. In addition, you can use the 12-watt USB-A port at the same time to charge a second phone or other device with any USB cable you already have.
MobileSpec Charging Bundles
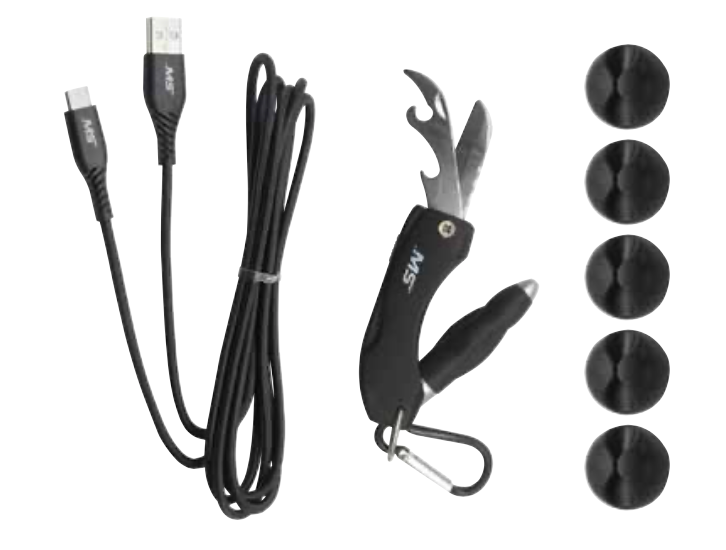
Let’s face it; your fancy smartphone is useless if not charged. And even the best, most powerful charger is of no value if you can’t get the juice to that same smartphone. The important link is the cable (yes, yes, we know, Qi allows wireless charging, but not every person has a compatible device), and MobileSpec delivers not just a good, solid charging cable but some much-appreciated accessories in its bundles.
Each bundle has a 6-foot-long Lightning to USB or USB-C to USB braided cable that has strain relief built-in, but other goodies as well. All three bundles include five cable organizers. Then you can get a bundle with a:
● Multi-tool that has a pen, knife, bottle opener and flashlight
● Phone cardholder for up to three cards
● Three-in-one phone mount (finger, stand or dashboard venter)
MobileSpec is a member of the RoadPro Family of Brands, and its bundles and other charging devices can be found at most truck stops and travel centers. Available online for under $13.
WeeGo Jump Starting Power Pack
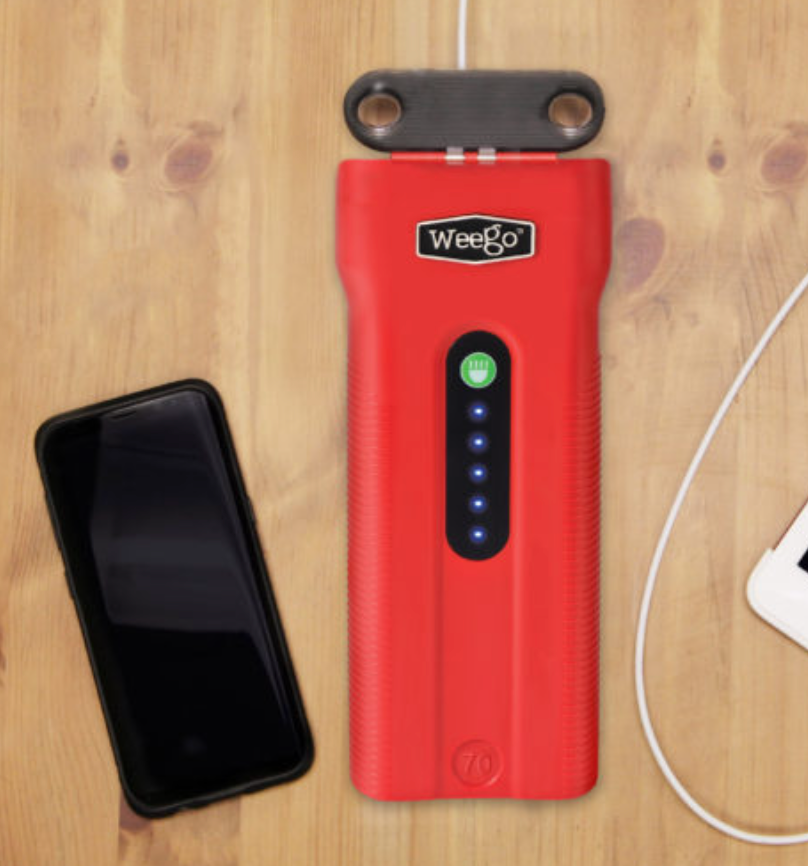
Don’t let the name fool you. This powerful battery can:
1. Jump-start your pickup or ATV
2. Recharge your smartphone or other device
3. Fit in the palm of your hand
That makes it ideal to keep in your truck’s cab. It literally packs a lot of power and takes up little valuable space.
WeeGo makes several power packs (including the Crankenstein, which is suitable for jump-starting duties at jobsites and repair shops), and includes the 44.1.
WeeGo’s new 44.1 weighs just a pound and a half, but its lithium-ion battery delivers 440 cranking amps, so you can jump-start most vehicles. The $129 unit also has a 12-volt port, a fast-charge USB port, and doubles as a flashlight with 500 lumens of illumination.
nker 24W Three-Port USB Portable Solar Charger
Anker is well known for producing reliable, affordable chargers and other digital devices. Among them is a solar charger; the Anker 24W 3-Port USB portable solar charger includes a foldable CIGS (thin-film) solar panel.
It’s suitable for iPhone 12/SE/11/XS Max/XR/X/8, iPad, Samsung Galaxy S20/S10/S9/S8. The solar panel’s three USB ports share a total 21W output, allowing you to simultaneously charge up to three devices. When you’re not charging, the PowerSolar folds away for easy storage. The built-in storage compartment can hold cables or small mobile devices. It comes with an 18-month warranty.
Available online for $79.99.
myCharge HubMax 10050 Portable Charger
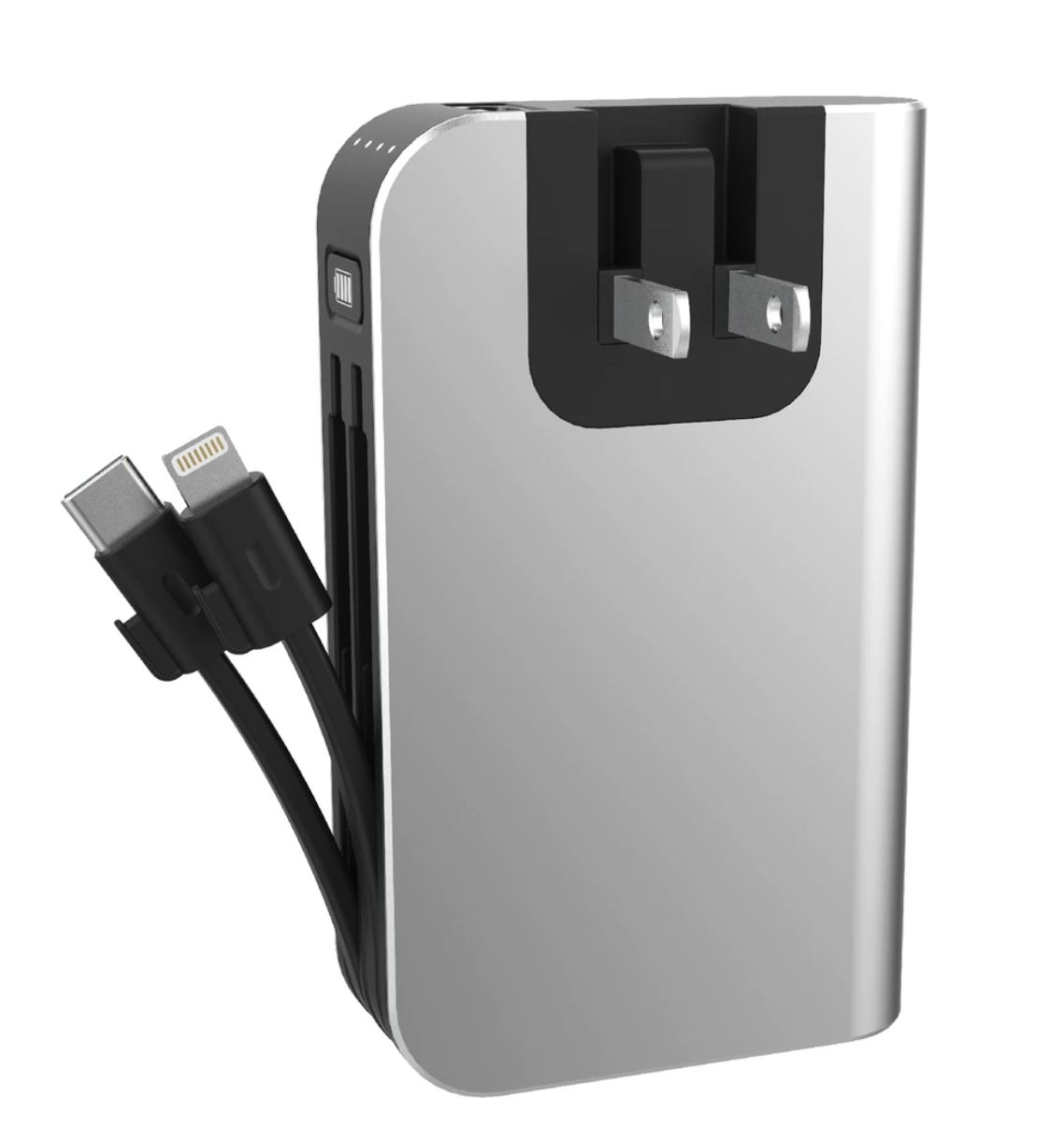
The myCharge HubMax 10050mAh portable charger has an integrated Apple Lightning cable, an integrated USB-C cable and a USB port. It also has self-contained wall prongs so you can plug it into a wall socket or an inverter.
With a 10050mAh internal battery, the HubMax 10050 delivers up to 54 hours of charging power. It’s available online for $89.99.
Belkin Boost Charge Wireless Charging Stand
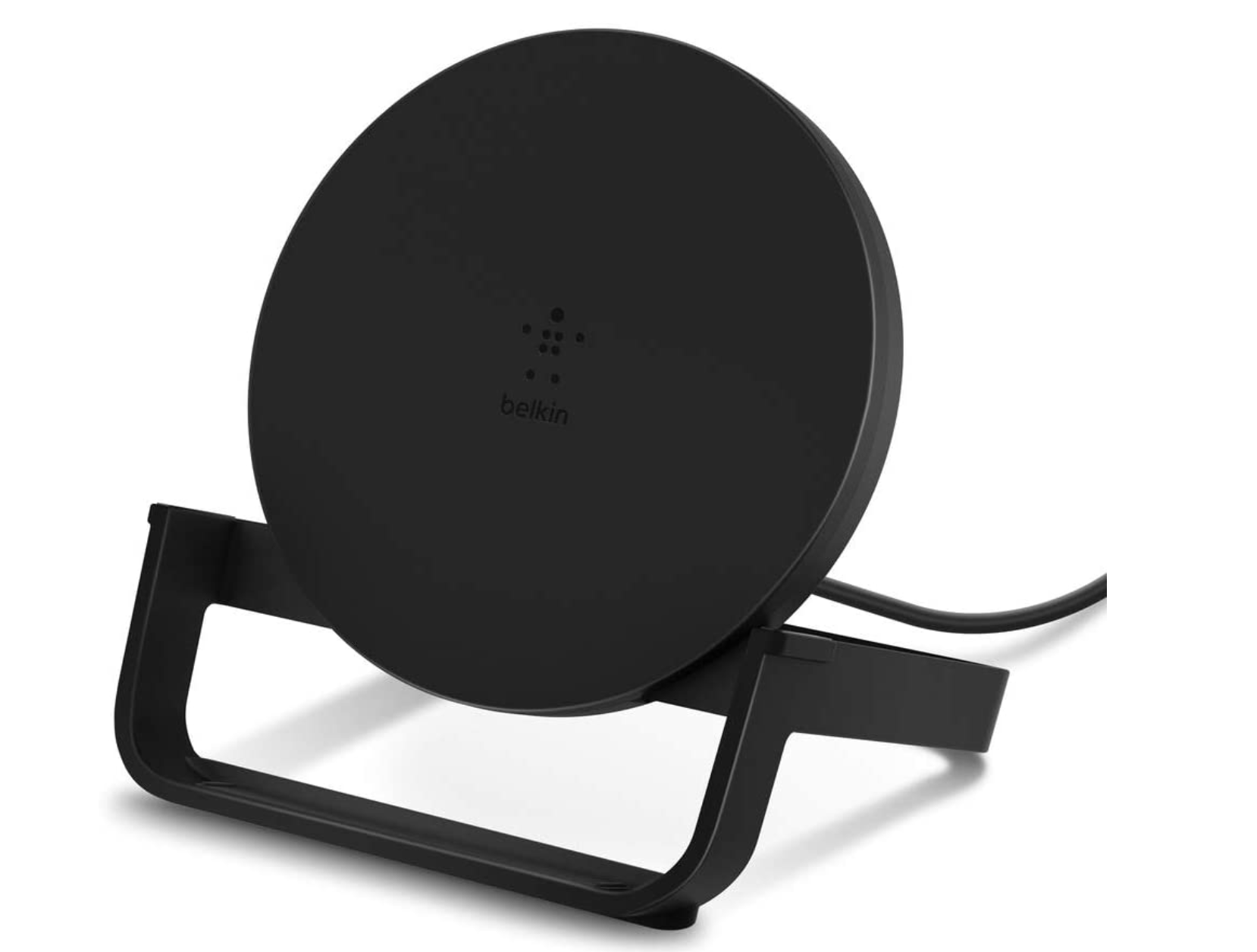
Belkin Boost WirelessThis wireless charging stand can reload a typical smartphone from empty to 50% in about an hour. It comes with a cable and wall plug and delivers a 7.5 W charging speed for iPhones and 10 W for Android smartphones.
The Belkin Boost is compatible with Qi-enabled devices including iPhones, Samsung Galaxy and Google Pixel. You can charge your phone in portrait or landscape modes.
Available online for $32.99.
Did you miss our previous article…
https://constructionosa.org/?p=314
Why Is Terex Trucks’ Articulated Truck Line Now Called Rokbak?
When Volvo Group changed the name of its Terex Trucks articulated truck line to Rokbak earlier this month, it represented the first time the company had created an entirely new brand, says Paul Roberts, Rokbak managing director.
North American dealer input played an integral role in the rebranding.
RobertsVolvoAfter the dust settled following Volvo’s 2014 acquisition of Terex’s articulated and rigid-frame truck lines, “we started having a dialogue with our dealers and customers asking how they felt about the brand and what it should look like,” Roberts tells Equipment World.
Volvo had changed the division name to Terex Trucks with the understanding it would be a step along the way to new identities. (The rigid frame trucks directed primarily at the mining and quarry segments are now Volvo branded; both truck types are manufactured in Motherwell, Scotland.)
And with Terex now concentrating on lifting, material handling and processing, “there was quite a lot of separation from that brand,” Roberts says. “And after quite a few years of Volvo ownership, there was still some confusion in the marketplace regarding who we were. Was it still part of Terex or part of Volvo? Did Volvo buy Terex?”
About three years ago, Volvo started to delve into the Terex Truck artic product branding, asking dealers if it was time for a change. “The answers were very clear: we had to start thinking about where the brand should go,” Roberts says. “We sampled a few names with some key dealers. We wanted to convey that this is a strong, simple product that’s as solid as a rock.”
At the forefront in this effort was the North American articulated truck market. “The North American market is hugely important,” Roberts says. “In some years, it makes up 50% of the world market for articulated haul trucks, which can be around 8,000 units. North American customers and dealers really know the product and its applications.”
Rokbak artics are distributed by around 30 North American independent multiline dealers and not through the Volvo CE dealer network, which, of course, distribute Volvo’s popular artic line. “We keep the brands separate,” Roberts says. “It’s a different platform and design.”
Volvo says the two Rokbak models, the the 30.9-ton RA30 and the 41.9-ton RA40, offer better fuel economy, lower emissions, improved safety and greater durability than the previous Terex Truck models.Volvo
Roberts points out that the articulated hauler space has relatively few competitors. He sees two types of customers: those looking for feature-laden premium products and those wanting simpler products. Rokbak products would tend to appeal to smaller to medium-sized earthmoving contractors. Top Rokbak markets are Florida, the Carolinas and Texas. The division is also looking to expand in Georgia and some areas in Canada.
Today’s supply-chain problems, however, have created interest in Rokkbak trucks outside its usual customer base, says Roberts. It’s a two-edged sword, however, since the division also faces similar supplier issues as other OEMs.
Volvo says the two Rokbak models, the the 30.9-ton RA30 and the 41.9-ton RA40, offer better fuel economy, lower emissions, improved safety and greater durability than the previous Terex Truck models, TA300 and TA400. For artics going to the European market, Europe’s Stage 5 engine requirements also prompted major changes in the machine control, intake and exhaust system that will not be part of the North American product.
Volvo traces the Rokbak’s lineage to 1934 when Euclid Road Machinery built what Volvo calls the world’s first off-road truck, the Model 1Z. The trucks have been made in Motherwell, Scotland, since 1950. General Motors bought Euclid in 1953 and renamed its earthmoving division “Terex,” from the Latin “terra” (earth) and “rex” (king). Terex became independent of General Motors in 1987, was bought by North West Engineering in 1992, forming Terex Corporation. Volvo Group then bought the off-road truck line from Terex in 2014.
Did you miss our previous article…
https://constructionosa.org/?p=310