Home » Articles posted by Tessa Sanderson (Page 6)
Author Archives: Tessa Sanderson
Massive I-80 Project Prepares to Take Off for Largest U.S. Inland Port
Advance construction on a $1.2 billion interstate project to improve access to North America’s largest inland port is underway.
The rebuild of 16 miles of Interstate 80 in Will County is expected to take six years. The 50-year-old section is part of one of only three coast-to-coast interstates in the U.S. and sees 80,000 vehicles a day, with trucks making up one-fourth of that traffic, according to the Illinois Department of Transportation.
“With demand for freight projected to double in northeastern Illinois the next 20 years, Will County’s role as a transportation hub and the country’s largest inland port is critical,” said Illinois Transportation Secretary Omer Osman.
Advance work on I-80 began in June with a $47 million project to replace several bridges in Joliet, Rockdale and New Lenox and widen a section of the interstate. This project will reconstruct the U.S. 30 interchange, adding a third I-80 lane in each direction west from Interstate 355. Ahead of the Thanksgiving holiday, a third lane on Interstate 80 was opened in both directions in New Lenox as part of this project.
To speed up the I-80 rebuild, IDOT plans for construction, land acquisition and final engineering on sections to occur simultaneously. A section from Ridge Road to the DuPage River will be under construction starting next year, while land acquisition progresses and final engineering is completed on replacing the Des Plaines River bridges, IDOT says. In 2023, work will shift to the section between Ridge Road and U.S. 30. Construction of the Des Plaines River bridges and Center Street and U.S. 52/Illinois 53 (Chicago Street) interchanges will take place in 2026 and 2027.
The planned construction phases for the $1.2 billion, six-year I-80 rebuild project in Illinois.Illinois DOT
When it wraps up in 2027, the overall I-80 project will have:
Redesigned and rebuilt 16 miles.Added or extended auxiliary lanes to improve safety and reduce congestion.Rebuilt or improved Interchanges at Interstate 55, Illinois 7, Center Street, Chicago Street, Richards Street and Briggs Street.Built a new flyover ramp linking southbound I-55 to westbound I-80 to improve traffic flow and safety. Rehabilitated or replaced more than 30 bridges.Built 8 miles of sound walls to protect nearby neighborhoods from traffic noise.Built bike and pedestrian paths.
“These overdue improvements will not only make it safer for commercial drivers, but for the thousands of families who rely on I-80 to commute to work, drive their kids to school and move safely through their daily lives,” said Governor JB Pritzker.
The I-80 project is being funded by Rebuild Illinois, the largest capital program in the state’s history. The $33.2 billion program was enacted in 2019, and the state’s gas tax was doubled to pay for it. The program focuses not only on roads and bridges but transit, waterways, freight and passenger rail, aviation, and biking and walking traffic, according to IDOT.
Did you miss our previous article…
https://constructionosa.org/?p=1082
A Dozer from Doosan?: Here’s the Sneak Peek (Video)
Known primarily in the U.S. for its excavators and wheel loaders, Doosan is entering new territory in construction equipment with its first ever dozers.
Also unusual for the South Korean company is that the new dozers will make their world market debut in the U.S.
Doosan unveiled a “pre-prototype” of the DD100 dozer recently at the company’s testing grounds near Tucson, Arizona. (A video of the dozer in action can be seen at the end of this story.)
The dozers are being developed and built in South Korea and will be shipped to the United States. A 10-ton model is expected to arrive in the third quarter next year. A 13-ton model is slated for mid-2023.
“It’s something dealers have asked for, to help expand their business and help with their rental fleets,” said Aaron Kleingartner, Doosan product and dealer marketing manager, during a media event in Arizona. “We’re excited to see what this particular product category can do for us.”
Preliminary specs on the DD100 dozer are likely to change, but so far it runs on a 122-horsepower Doosan diesel engine that does not use a diesel particulate filter.
The company hopes to capture a portion of the $2.1 billion U.S. dozer market, 45% of which is made up of machines under 140 horsepower, Kleingartner says. The dozer additions will also give Doosan dealers and their customers a “one-stop shop” for their construction equipment needs, he said.
Doosan’s DD100 prototype dozer has a 122-horsepower engine with no diesel particulate filter.DoosanKleingartner summed up the company’s goals for the new dozers:
“We want to make sure we have low maintenance costs, superior power and traction, excellent visibility, and safe and easy operation. Those things are all going to be the requirements for us to be able to provide the opportunity for our customers to make the switch into this new product category.”
The cab, with lots of glass for better visibility, will be similiar to the company’s new line of excavators and wheel loaders. Controls will also be similar. Visibility is further increased by a narrow front engine box, and Doosan hid the air-intake pre-cleaner under the hood so it won’t block the operator’s view.
Other standard features include an 8-inch touchscreen display, rearview camera, front and rear LED lights, and rear side wiper blades. It will have keyless entry and push start.
Doosan sought to improve operator visibility with lots of glass and by moving the air-intake pre-cleaner under the hood.Equipment WorldThe dozer blade will be six-angle, variable pitch. The standard blade will have a capacity of 2.9 cubic yards, and for the LGP model, 3.4 cubic yards.
The company says it has an agreement with Trimble to install mastless 3D machine control as an option. The controls will be standard electro-hydraulic, and the operator will be able to adjust control speed.
Mooyoung Park, Doosan engineering manager, said Doosan was mindful of the U.S. labor shortage and is designing the dozers to be easy and comfortable to operate. Safety features include a seat with an automatic cut-off sensor, so when the operator stands up, the machine will stop.
Doosan hopes to capture a share of the under-140-horsepower dozer market with new models for 2022 and 2023.DoosanThe DD100 model, which the company rolled out at its Arizona testing grounds, is expected to undergo changes in the development process before mass production.
The concept model was a low ground pressure version weighing 25,000 pounds. The standard model will weigh about 22,000.
“So our machine is a little bit heavier than the competition, and being a heavier machine,” Park said, “you’ll have more tractive effort to accommodate the power.”
Other preliminary specs on the DD100 prototype:
Blade height: 3 ft. 7 in. Blade width: 8 ft. 10 in. Blade angle: 22.5 degreesDrawbar pull: 33,721 pound-feetTrack length: 7 ft. 7 in.Travel speed, max: 5.7 mph
Contractor of the Year Finalist: W.F. Delauter Grows from One Dozer to 135-Piece Fleet
Kirby Delauter’s father, Russ, jokingly refers to the firm he and his father, Willie, formed in 1955 as a “one-horse operation.” Change that from one horse to one dozer, which the father-son team used to perform residential and commercial grading.
Now, far from that one-dozer start, the company is run by third-generation Kirby Delauter and his wife, Tina Delauter. The $10 million to $12 million firm does a variety of work including site development, demolition, utilities, bridges and stormwater management in three states.
Kirby’s entering the firm wasn’t necessarily a done deal, however. After serving six years in the U.S. Army, “I didn’t know what I wanted to do, and I didn’t think I was college material,” Kirby recalls. He joined the family firm and proved so adept he became president in 1994.
And after working for several years outside the company, Kirby and Tina’s son William has joined the firm and is on his way to becoming the 66-year-old company’s fourth generation. A licensed civil engineer, William has “the education to take this as far as he wants to take it,” Kirby says.
“After being on the design side, now I’m getting more of the construction side,” William says. But keep in mind he did grow up working in the family business before college, and Kirby says he “knows what it’s like getting dirty in the ditches.”
Great Recession
Like many in this industry, the Great Recession hit the company hard. “It’s something I’ve never seen before,” Kirby says. “It took us from around 65 employees down to 16.”
“You just worked through it because that’s all you could do,” he adds. “You learned a lot of things that you’ll never find in a book.”
“That showed me more about what he’s made of than anything because he handled it in a way that I couldn’t have,” says Russ.
The experience has prompted an emphasis on measured, steady growth. “We could be three times the size we are right now,” Kirby says, “but I want to grow the company responsibly.” He expects the business to increase revenues to $13 million to $15 million this fiscal year, which ends in March.
Sharp eye
W. F. Delauter crews on the $3.6 million Gas House Pike Bridge in Frederick, Maryland.Equipment WorldPart of that responsible growth is keeping a sharp eye on equipment needs. “We run a little leaner now,” Kirby says. “If we don’t need something, I may sell it and then think about renting it.”
Kirby frequently uses RPOs and buys used if it’s a machine he expects to put less than 1,000 hours a year on. “Excavators, loaders and dozers are our frontline pieces, so I’m either going to buy them new or low-hour used,” Kirby says. The firm has around 135 major pieces of equipment.
In addition to the heavy machines, W.F. Delauter has seven compact track loaders. “They’re powerful and they get the job done,” Kirby says. “With a blade on them, you can sometimes use them as a default for a D4. It won’t push as much, but it gets around better. And we’ve had zero problems with them.”
Clients notice the appearance of W.F. Delauter machines on their jobsites. “His equipment is always in tip-top shape,” says Vinny Flook, owner of Vinny’s Towing, who has done several projects with the company.
The company has three full time mechanics, including one who specializes in engines. “We do most of our work in-house, such as reinstalling refurbished undercarriages,” Kirby says. A fuel/lube truck services the company’s jobs.
Learning that a local college had a Cat simulator but no instructor, Kirby raised his hand and taught equipment operation evenings and weekends this past semester. He took the students to one of his jobsites where they spent eight weeks operating equipment.
“All of the students passed the class,” Kirby says. He didn’t stop there: he helped them create resumes and gave them contacts. All found employment at $22 to $24 an hour within weeks of completing the course.
Tina joined Kirby in the office around eight years ago and handles business development, HR and manages the company’s 60-construction-dumpster roll-off division. The division developed out of W.F. Delauter’s need to haul construction debris off its own sites and now generates about $700,000 a year.
“We’re also looking at marketing recycled construction materials to other contractors,” Tina says.
Family first
The International TD6 dozer that Willie and Russ Delauter used when starting W.F. Delauter now sits at the entrance to the firm and serves as the backdrop in this company photo.Equipment WorldThe company has around 70 employees, including five utility crews, two grading crews and a concrete crew. “I’ve always felt that good people attract good people,” Kirby says.
“We feel that family comes first,” Tina says. “I think that gives them an incentive to stick with us. And once you feel like you’re part of the team, you’re locked in with the group. We always tell them there’s room to grow. You might be a laborer now, but if you can jump on the backhoe and learn, for example, there’s a lot of potential to grow.”
Tina and Kirby also keep an eye on local labor rates, Kirby says. “I ask myself, ‘Are we going to keep good people and do people believe in us enough to sustain that?’” he says.
“It’s really been an honor for us to continue the legacy that Russ and Willie built from the ground up,” Tina says.
Client appreciation
You get a sense of both the legacy and the future of W.F. Delauter when you talk to its clients.
“They always stand behind their word,” says client Steve Oder with Cavalier Development. “I could do a handshake contract with them and be perfectly comfortable. There’s not many of those around anymore.”
“Concerns were quickly put to rest after seeing how conscientious, knowledgeable and skilled [their] employees were throughout the duration of the project,” says Gale Engles, bureau chief for the Carroll County, Maryland, Bureau of Resource Management.
“One thing that’s really impressed me, especially considering the size of his business, is how much he’s available and how responsive he is,” Flook says. “If it comes out his mouth, it’s golden.”
Did you miss our previous article…
https://constructionosa.org/?p=1069
Product Roundup: Komatsu harvester and forwarder feature ground-gripping traction
There is probably no tougher environment for equipment than forestry, and Komatsu’s two new purpose-built machines, the 931XC-3 harvester and 855-3 forwarder, are made to stand up to these gnarly conditions.
Designed for maneuverability in everything from thinning operations to felling big timber, the 931XC-3 harvester balances power, torque and fuel economy to optimize low-speed operation with a high torque backup when needed. The machine’s eight-wheel-drive traction and smooth ride come courtesy of what Komatsu calls its “Comfort Bogie” drive system. The bogies oscillate to keep tires on the ground, following the terrain closely while maintaining a high clearance. Additionally, a fixed rear-axle design reduces rear ground pressure.
The harvester’s automatic cab/crane leveling system keeps your operator in the best possible position to work comfortably throughout the day. An automotive-quality cab features heated and cooled meal storage, a big front window for visibility, an ergonomic seat and climate control.
Designed with a high departure angle for climbing obstacles, the Komatsu 855-3 forwarder offers an optional blade for stump removal.KomatsuThe 14-metric-ton Komatsu 855-3 forwarder also operates on Komatsu Comfort Bogie axles with a high portal offset and V-shaped frame for ground clearance. For ground or stump leveling, an optional heavy-duty stacked blade is available. Mounted with a high angle of departure for climbing obstacles, there’s no interference between blade, battery boxes or hood guard. Operators can monitor and control everything from the engine and crane to the transmission and service ladders with the MaxiXT system. And operator-specific controls can be fine-tuned to achieve the finesse and speed each operator prefers.
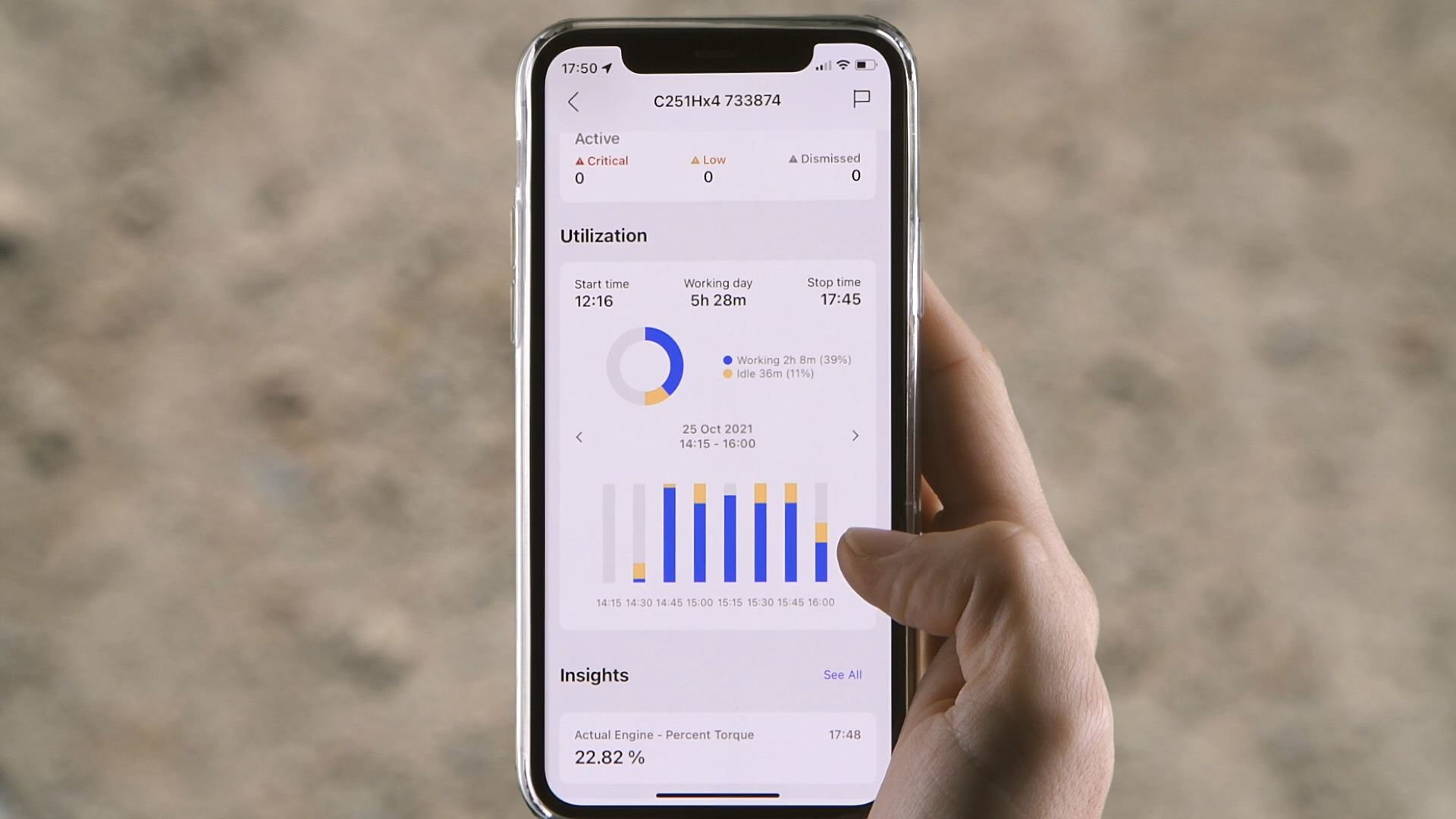
Keep tabs on your AUSA machines with cloud-based monitoring.AUSANew software gives customers telematics info for AUSA vehicles
AUSA has announced the global launch of its AUSAnow fleet manager, an online fleet control solution. With this new digital service, AUSA is offering its customers a product to improve their efficiency and profitability by monitoring their machines with mobile phones or computers.
The new software communicates real-time information about maintenance requirements, technical and performance issues and any unexpected movement of machines.
Machine information is stored in the cloud, so AUSAnow can be accessed anywhere you can connect to the internet. The new system will allow users to view and create their own personalized charts, obtain in-depth information about the operation of their machines and make decisions that are based on detailed information.
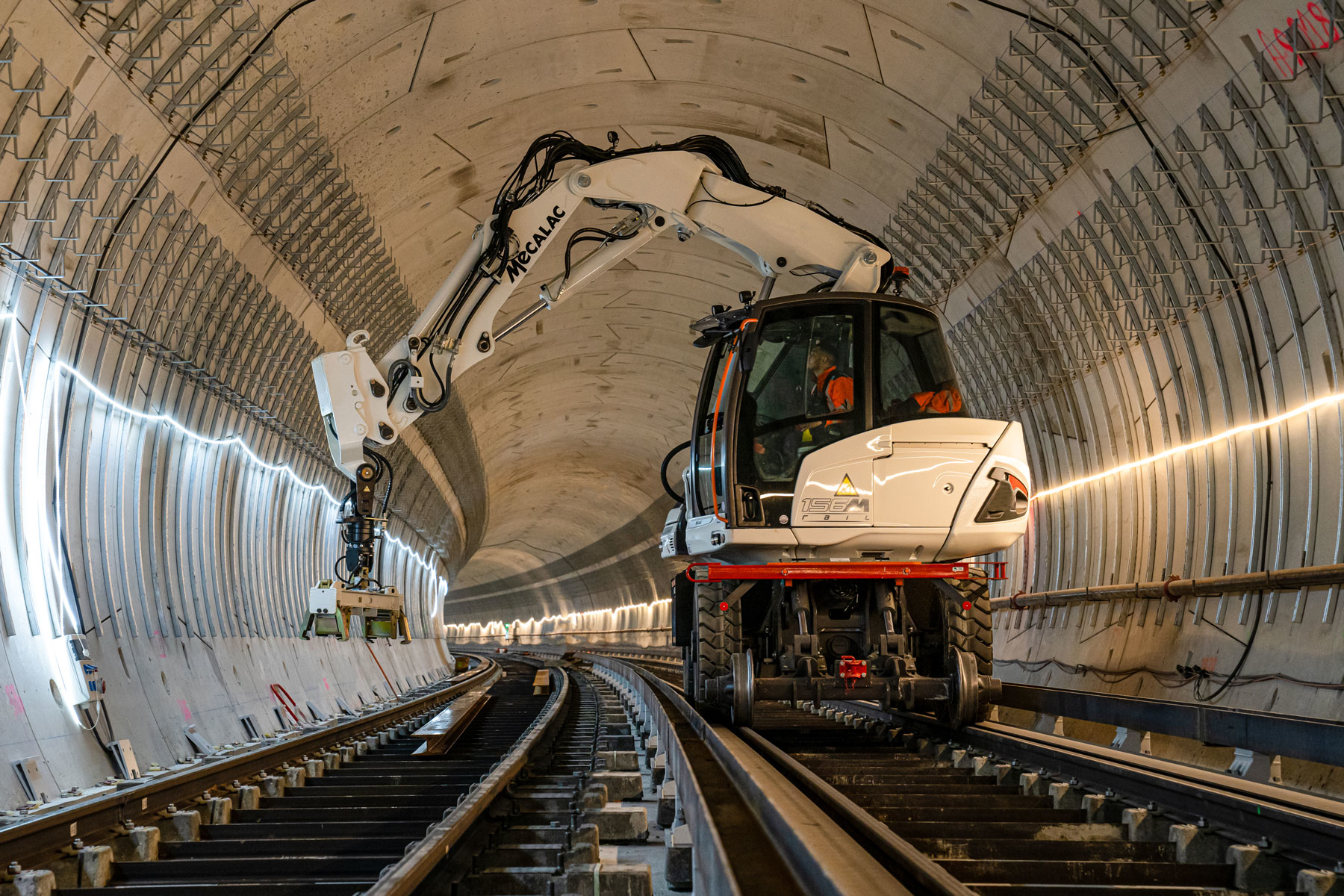
Mecalac 156MRailMecalacMecalac debuts new MRail-Series, a dedicated line of machines for the rail industry
Purpose-built for right-of-way maintenance or the construction of new tracks, Mecalac’s four new MRail-Series machines offer advanced safety features and performance tailored to meet the requirements and track sizes of public and private railways, light rail and subway networks.
The two tracked models, 106MRail and 136MRail, are based on the MCR crawler skid excavator concept. The 10-ton 106MRail can travel up to 6.2 mph on ground and 14.3 mph on rails. The 13-ton 136MRail offers ground speeds up to 5.6 mph and rail speeds as high as 12.4 mph.
Both models offer 360-degree rotation. Optional rear and side cameras provide extra safety, visibility and precision when working in-between tracks, in tunnels or confined spaces.
Based on the MWR wheeled excavator, the 156MRail and 216MRail models provide solutions tailored to rail networks, different track sizes and available workspace. The 156MRail is ideal for users looking for a machine to work on subways or private tracks without the expensive features required by rail regulations. The 156MRail’s compact design provides good visibility for work in hard-to-reach places. It boasts travel speeds up to 21 mph on the ground and 18.6 mph on rails.
Built for the toughest rail jobs, the 216MRail model brings agility and maneuverability to users looking to complete projects on national and urban railways. With the greatest boom reach of the MRail models, the 216MRail can reach up to 24 feet 7 inches. It travels at speeds up to 18.5 mph on both ground and rails.
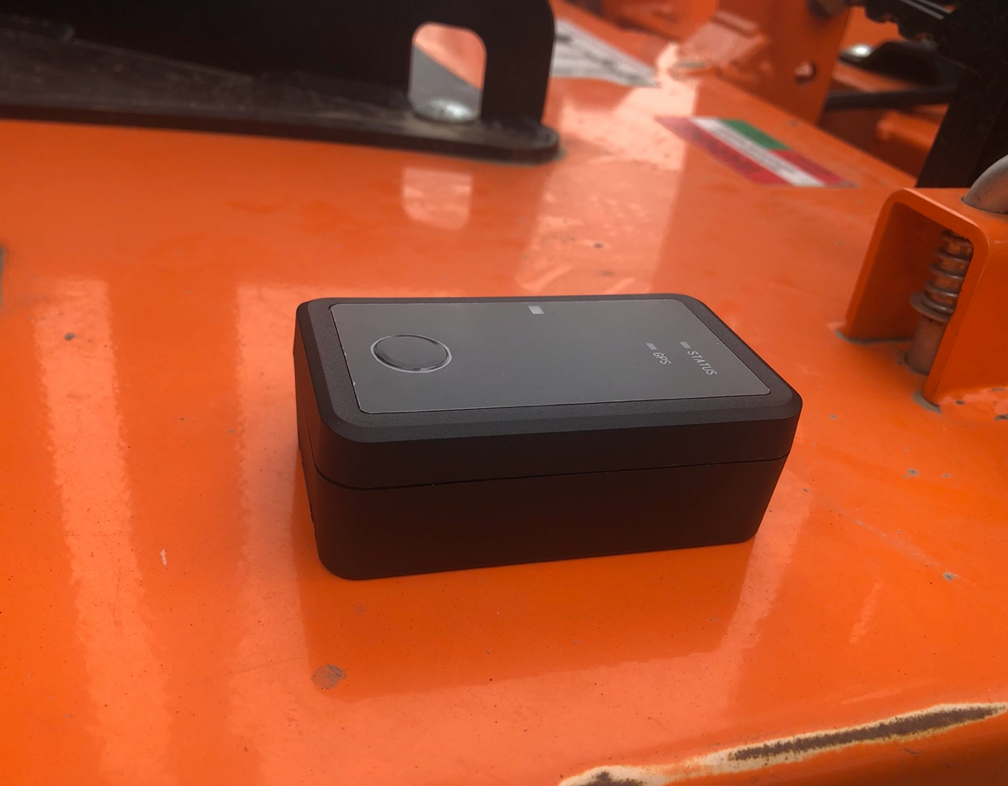
The hidden installation and a tamper-proof design of GPS Trackit’s monitoring system enables you to keep tabs on unpowered equipment.GPS TrackitStop trailer theft with GPS Trackit monitoring
According to the International Risk Management Institute, only 10 to 15 percent of stolen equipment is ever recovered. One solution is GPS-enabled electronic monitoring. The recently announced GL500MG tracker from GPS Trackit monitors truck trailers and cargo to deter theft and assist in asset recovery.
GPS Trackit’s GL500MG protects unpowered assets including construction equipment, freight trailers, flatbed trailers, freight containers, generators, tool storage boxes, and recreational equipment.
The device features a five-year, onboard battery and durable housing to help construction companies, carriers and trucking companies locate and control their trailers around the clock. Geofences provide alerts whenever an asset leaves a pre-set area. A user update button immediately shares the GL500MG’s GPS coordinates to help you and law enforcement find the stolen asset.
Did you miss our previous article…
https://constructionosa.org/?p=1063
Honda’s Autonomous Work Vehicle Put to the Test at 1,000-Acre Jobsite (Video)
Every newbie who ever worked in construction knows the grunt work of having to haul material around the jobsite. Well, good news newbies.
Honda has a prototype robot that someday may put an end to this backbreaking tradition. At a large-scale Black & Veatch solar installation jobsite in New Mexico, the company successfully tested the latest prototype Honda Autonomous Work Vehicle (AWV). (Check out the video at the bottom of this story.)
And perhaps the coolest thing about the Honda AWV project is that it is actively soliciting contractors who want to help design the next version of the robot. Companies interested in testing the Honda AWV in their work environment can contact Honda at: [email protected].
Hefty payloads
During the month-long field test in New Mexico, the second-generation prototype of the fully electric Honda AWV performed a range of functions including towing activities and transporting construction materials, water and other supplies to pre-set destinations within the worksite.
The vehicle carried payloads of nearly 900 pounds, and in a separate use case, it towed a trailer hauling more than 1,600 pounds. While Honda previously tested an earlier generation of the Honda AWV, this field test was the first to deploy multiple units working collaboratively to support construction use cases.
Honda has been tinkering with the AWV platform for a while. It was introduced as a concept at the 2018 Consumer Electronics Show in Las Vegas. You can see what we wrote about the first version here: Honda unveils autonomous construction robot, wants your input on what to do with it
GPS guidance
The current version of the Honda AWV employs a suite of sensors to guide the unit autonomously, using GPS for location, radar and LiDAR for obstacle detection and stereoscopic (3D) cameras for remote monitoring. The vehicle also can be operated by remote control.
To validate the capabilities of the Honda AWV, the company selected a Black & Veatch’s solar energy construction site where support structures for solar panels are laid out in a grid pattern at regular intervals over a thousand acres. The site was an ideal environment to test the ability of the Honda AWV to stop at precise points along a pre-set route.
Cloud-based directions
Honda produced a high-definition map of the site that allowed Black & Veatch operators to precisely set start and stop points for multiple Honda AWVs using a cloud-based app interface that runs on tablets and PCs. The vehicles successfully delivered materials and supplies along a calculated route and stopped within centimeters of their pre-set points.
The field test also demonstrated the viability of the Honda AWV battery system to support energy-intensive sensors and provide vehicle propulsion, while operating up to eight hours in a high-temperature environment.
Based on the capabilities verified in this field test, Honda says its AWV will be capable of providing a wide range of services to a variety of industries that need a rugged off-road autonomous solution, especially where workforce constraints and safety concerns make other solutions impractical. The ability to operate autonomously, or with remote control, and carry large payloads, along with the potential to add attachments and tools, make the Honda AWV a suitable platform for many work environments.
Efficiency and safety
The goal of the project, according to Honda, is to create a rugged and durable off-road side-by-side platform with advanced autonomous technology capable of being deployed in a variety of dynamic work environments.
“We believe the Honda AWV has the potential to bring greater efficiencies, higher levels of safety and better environmental performance to the construction industry and to other industries seeking an autonomous off-road solution,” says Kenton Williams, project lead for the Honda AWV. Honda has not announced commercialization plans for the AWV yet, but is continuing to advance the platform through field testing.
You can watch a video below of the Honda AWV doing its thing:
Honda AWV Specs
Dimensions: 9 feet 6 inches long; 8 inches high; 4 feet 11 inches wideUnladen weight: 1,590 poundsMax load capacity: 880 poundsTowing capability: 1,653 pounds (including trailer)Min. turning radius: 12 feet 9 inchesRange: 27.9 miles depending on use case Charge time: Up to six hours
Did you miss our previous article…
https://constructionosa.org/?p=1060
Back on Track(-ish): 2022 Construction Equipment Trade Shows and Events
After two years of disrupted industry events, construction equipment trade shows and conferences will be making their (somewhat normal) return in 2022.
Earlier this year, Bauma announced it would be pushing show dates from April to October 2022, citing ongoing uncertainties due to the global pandemic. Some major OEMs have since pulled out of the show, including Volvo Construction Equipment and JLG. Caterpillar corporate announced German dealer Zeppelin would exhibit in its place.
The American Rental Association will not hold a traditional 2022 ARA Show due to the proximity of its 2021 event, which was pushed from February to October. Show organizers have instead announced an innovation and technology adoption conference with exhibits.
Mark your calendars. Here is the slate of construction industry events for 2022:
Associated Equipment Distributors (AED) Summit
Location: Orlando, Florida
Dates: January 17-19, 2022
World of Concrete
Location: Las Vegas, Nevada
Dates: January 18-20, 2022
National Asphalt Pavement Association (NAPA) Annual Meeting
Location: Scottsdale, Arizona
Dates: January 23 – 26, 2022
Underground Construction Technology International Conference & Exposition
Location: Fort Worth, Texas
Dates: January 25-27, 2022
Land Improvement Contractors of America (LICA) 2022 Winter Convention
Location: San Antonio, Texas
Dates: February 15 – 19, 2022
National Pavement Expo
Location: Charlotte, North Carolina
Dates: February 23 – 25, 2022
National Demolition Association (NDA) Annual Convention & Expo
Location: San Diego, California
Dates: February 26 – March 1, 2022
American Rental Association Innovation Conference & Exhibits
Location: Dallas, Texas
Dates: March 9-10, 2022
National Ready Mixed Concrete Association (NRMCA) Annual Convention
Location: San Antonio, Texas
Dates: March 15 – 18, 2022
Associated Builders and Contractors (ABC) 2022 Convention
Location: San Antonio, Texas
Dates: March 15 – 17, 2022
Equipment World’s Contractor of the Year Awards
Location: Las Vegas, Nevada
Dates: March 17-20, 2022
World of Asphalt
Location: Nashville, Tennessee
Dates: March 29-31, 2022
AGG1 Aggregates Academy & Expo
Location: Nashville, Tennessee
Dates: March 29-31, 2022
North American Society for Trenchless Technology (NASTT) 2022 No-Dig Show
Location: Minneapolis, Minnesota
Dates: April 10 – 13, 2022
Equip Expo (formerly GIE + Expo)
Location: Louisville, Kentucky
Dates: October 19 – 21, 2022
Bauma
Location: Munich, Germany
Dates: October 24 – October 30, 2022
Trimble Dimensions
Location: Las Vegas, Nevada
Dates: November 7-9, 2022
Did you miss our previous article…
https://constructionosa.org/?p=1048
Cat Command Expands to 374, 395 Excavators
Operators can now dig, lift and track large excavators from a safe distance at hazardous jobsites or remote locations. Cat Command for Excavating is now available for the 374 and 395 models.
The remote-control system – which can be operated from onsite or hundreds of miles away – provides contractors with three primary benefits:
Enhanced safety: Suitable applications include working on steep slopes, soft underfoot conditions, hazardous material handling and demolition. It also allows production to restart immediately following disruptive processes such as blasting in quarry applications. Increased productivity: Operators can move from one machine or one jobsite to the next with the touch of a button, saving time moving between locations and reducing the chance of falls from climbing on and off machines.A solution to combat the skilled labor shortage: Operators with physical limitations can comfortably run a machine from a station.
Both line-of-sight and non-line-of-sight operating options are available for Command for Excavating.
The Command console is ideal for short-term or emergency remote operation and is worn via a shoulder harness.
“Say you’re running in a safe environment, but you’ve got some work to do on a slope where there is some opportunity for danger,” says Cat product marketing consultant Mike Lenzie. “[The operator] can jump out, switch to remote-control mode, run it with that line-of-sight Cat Command console for an hour or two, and switch back to manual mode and continue operating.”
Using either a 900 MHz or 2.4 GHz frequency communications protocol, the console offers a machine control range reaching up to 437 ft. Built-in safety features stop all excavator movements if the remote shutdown switch is pressed, wireless communication is lost, or the console is tilted more than 45 degrees.
The Command station is a long-term solution for non-line-of-sight operation in an office onsite or a distant location.
“The station itself is set up with a seat that you would see in a Caterpillar piece of equipment. It has displays set up in front of you that mimic the exact display you would see inside the cab,” says Lenzie. “Then we have the ability to set up cameras not only on the piece of equipment but also at the site it’s running to give the operator the ability to visualize what he or she is doing.” Operation distance is limited only by the capabilities of the wireless network.
Users can control up to five different machines from the same or different locations, reducing downtime for shift changes or the need to travel to the jobsite. A touchscreen monitor similar to the in-cab display offers precise machine control, and screen mounts positioned in front of the user provide easy view of the excavator’s camera feeds.
Standard machine technologies including Grade Assist, Swing Assist and E-Fence can be set, activated and deactivated remotely.
JCB’s New Electric 505-20E Loadall Telehandler Delivers Diesel-Like Performance
JCB has unveiled the 505-20E, a fully electric version of its Loadall telehandler. The new zero-emissions machine has a lift capacity of 5,250 pounds and 20 feet of lift height.
Dual electric motors power the machine, one for the driveline and the other for the hydraulic system. The 30-horsepower hydraulic system pushes a fixed displacement gear pump that delivers 21 gallons of flow per minute maximum.
The 96-volt lithium-ion battery holds enough charge to work for a full shift. Charging options include on- and off-board rapid charging. The 110-volt/16-amp on-board charger can fill the battery in 8 to 10 hours, and a 220-volt on-board charger is available as an option. JCB also offers a universal charger that can be used for a rapid top-up in as little as one hour.
The emissions-free operation of the JCB 505-20E is not only an environmental plus, it enables you to use the machine indoors, where diesel exhaust would be problematic. The battery power also drops noise levels dramatically — from an in-cab level of 92.2 decibels to just 66.7 decibels — less volume than a vacuum cleaner. To keep crews safe around this quieter machine, a white-noise reversing alarm is standard equipment. It is available in cab or canopy configurations.
At 5,250 pounds, the 505-20E is slightly lighter than its diesel counterpart, but the dimensions are the same: 12-foot 1-inch outside turn radius and an overall height of 6 feet 2 inches. Cycle times are likewise the same with no loss of performance, and it can be used with forks, a range of buckets and other JCB Loadall attachments.
Did you miss our previous article…
https://constructionosa.org/?p=1042
West Side Tractor Sales: Designing the Dealership of the Future
“I can truly say I have never worked with a dealer that’s so committed to their customer success, from sales, service support to ownership,” says customer Jon Kaye, who nominated West Side Tractor Sales for Equipment World’s Big Iron Dealer of the Year honor.
The vice president of equipment for Miller Bros. Construction in Archbold, Ohio, continues: “They truly build relationships with their customers, focusing on how they can help grow and bring efficiency to the customer’s business.” Kaye’s experience with West Side began during his time as fleet manager at Gallagher Asphalt in Thornton, Illinois.
That’s just the impact that West Side Tractor Sales, headquartered in Lisle, Illinois, is striving for as it navigates the highly competitive world of construction equipment.
“We make it very intentional to spend an incredible amount of time out with customers and listening to their problems,” says Brian Benck, vice president of sales and a third-generation owner. “We want to serve the person that buys one tractor every 10 years as well as offer tailored solutions to those customers that buy 100 tractors a year.”
West Side’s second- and third-generation family leadership team includes (l. to r.) Steve Benck, Diane Benck, Lauren Coffaro, Jen Snow, Brian Benck and Tom Benck.Established in 1962 by Rich and Mary Benck, West Side now serves as the John Deere dealer in more than 80 counties with 11 locations in Illinois, Indiana and Michigan. Six second- and third-generation owners – all deeply ingrained in the company’s day-to-day operations – now carry on the legacy: children Steve, Diane and Tom Benck and grandchildren Brian Benck, Jen Snow and Lauren Coffaro.
“My father picked a really good partner in John Deere in the ’60s that allows us to be where we are today,” says Diane Benck, vice president of general operations and second-generation owner.
That includes a shiny new headquarters with a state-of-the-art shop. (More on that in just a bit.)
“There’s so much opportunity to have organic growth within our footprint,” Diane says. “I’m not a big believer in buying a lot of territories. I’d rather do something really well, provide bottom-line returns while giving awesome customer service. Being twice as big and making half as much doesn’t serve any purpose. I don’t always think bigger creates the best customer experience, and that’s a priority for us.”
That’s not to say that West Side hasn’t had its share of geographical growth. Rich expanded in the ’70s to four locations in the Chicago area. The second generation added a fifth Chicago-area location and in 2010 acquired five Deere dealerships from Holt Equipment, adding 68 counties in Indiana and three counties in Michigan. New facilities have also been built in Bloomington and Terre Haute, Indiana.
The changing customer
A company that’s now in its third generation has had a front-row seat to changing customer expectations.
“Customers now have an on-demand mentality,” Brian says. “Whether it’s the sourcing of equipment or parts, customers have a much better understanding of their own efficiency, and we’ve had to tailor our model to on-demand. We have to have the inventory and have it ready to go.”
“I think we’ve gotten so much savvier about how we’re engaging customers,” says Lauren Coffaro, marketing and technology manager and third-generation owner. Social media has given the dealership the ability to get quality leads with people it didn’t have a relationship with before.
What hasn’t changed, however, is that relationships still matter, Diane says. “The basic relationship that we foster with those customers is still there.”
“Dealership of the future”
“We wanted the Lisle headquarters to be the dealership of the future,” Lauren says of the facility that opened last year.
“We put a lot of thought into our employee areas,” Diane says. And with an eye toward attracting more women, it put in separate locker rooms and a lactating room.
As it developed plans, West Side scrutinized shop processes, knowing the more time a technician spends working on a machine, instead of ancillary activities like parts runs, the less time the customer has to wait to get the machine back.
By using the vending machine, technicians are kept in the shop space and the process tightens up billing and inventory management.West Side Tractor SalesTo maximize efficiency, the shop has a vending machine that uses facial recognition to dispense commonly used parts such as zip ties, brake clean, and cleaning and grinding discs. The technician takes what he or she needs, types in a work order, and the supplies are automatically allocated. “By using the vending machine, technicians are kept in the shop space,” Lauren says, and the process tightens up billing and inventory management.
Each technician has a laptop; they can order parts and stay in the bay while parts are located and delivered to a mailbox at each bay, further eliminating wasted technician time. “Those lost minutes add up, especially in a facility as large as Lisle,” Lauren says. “Our service manager is also running a live screen, tracking all the work done each day and the time it is taking to complete a project.”
“We’ve only been in Lisle a year and the service sales are up 20%,” Diane says. The new facility also allowed West Side to add a certified Deere rebuild facility, including a clean room.
The key to staying a leader
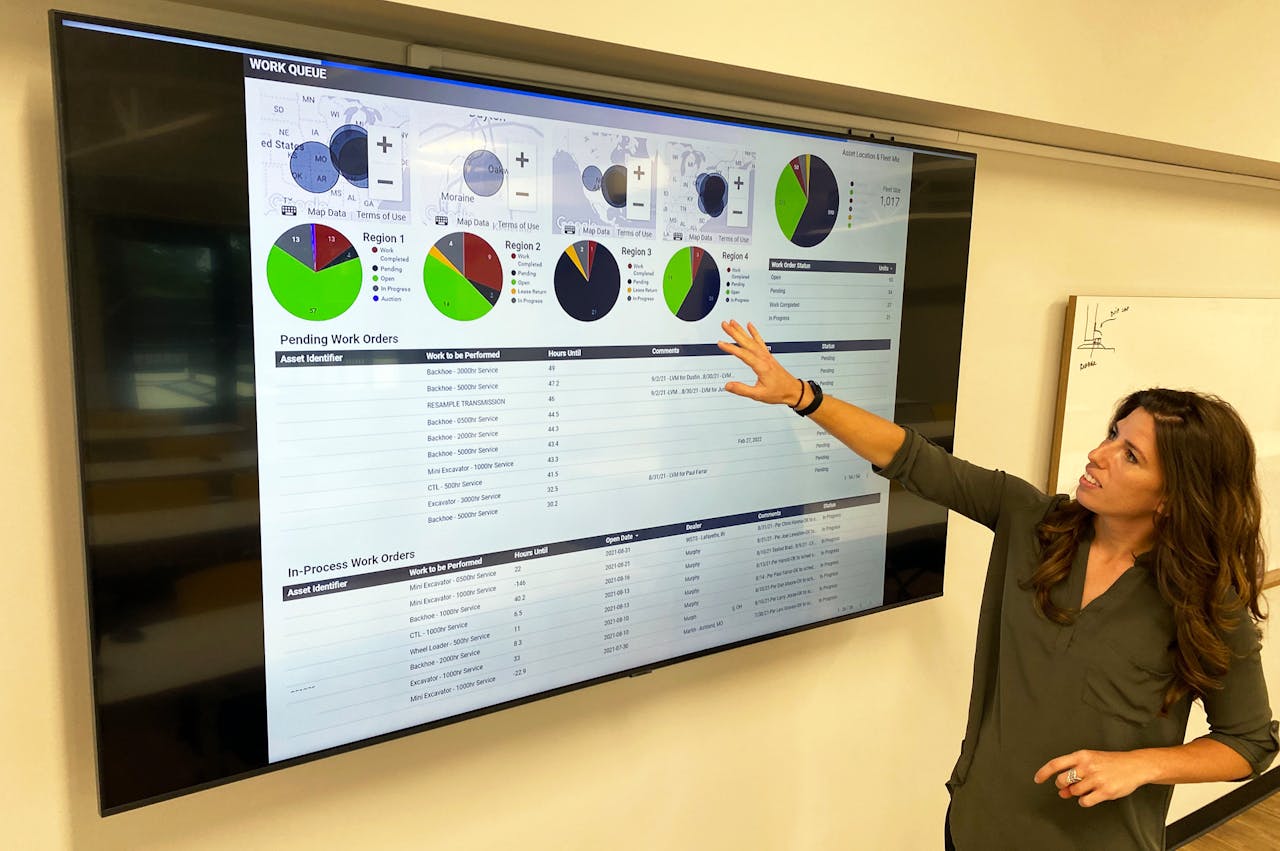
With West Side’s new fleet services initiative, West Side says it offers to “do the heavy lifting in managing our customer’s data.”West Side Tractor Sales
“We’re working really hard on our technology solutions side,” Diane says. “The use of technology is so key to staying ahead of the competition. We usually know what’s going on with their machine before they know it, and we’re calling them proactively.”
West Side established its technology division in 2015. It now offers fleet monitoring (remote support, proactive alert management and JDLink hardware sales), the positioning products (SmartGrade, grade control, off-machine instruments and drones) and its new fleet services initiative.
With fleet services, West Side offers to “do the heavy lifting in managing our customers’ data,” Lauren says. The department grew out of a customer’s request to manage their PMs in different U.S. locations. West Side now manages their equipment data and examines their lease structures. “We know we can apply what we learned in that process to other customers,” Lauren says.
One example is West Side’s new idle time reduction program. “The goal is to grow it into a portfolio of reporting products that we can sell on a subscription basis,” Lauren says.
“Sometimes it’s just listening and then making the extra effort to try to address some things that may not necessarily relate to an equipment sale that helps tie and pull that relationship closer,” Brian adds. “This is an effort to really understand what projects we can work on for customers to help them improve their operations. I see that as a total game changer that most dealers aren’t doing today.”
Noting that it was getting regular requests for basic training on its positioning equipment, West Side also started putting QR codes on this equipment this year, allowing operators to link directly into the dealer’s website and grab a quick tutorial video.
It used to be that the customer relationship was wrapped up in the dealer rep. “We have found that the most successful customer relationships are not about that one person but about creating a team that can jump in to support the customer in many different ways,” Lauren says. “We have true experts, whether in service, technology or production-class machines, that can create that world-class customer experience.”
Overcoming supply-chain shortages
Today’s global supply chain issues are ever-present in frontline operations such as West Side.
“We’ve always been a dealer that stocked more on the heavy side, so going into this we were perhaps in a better position than maybe a lot of dealers,” Brian says. “We kept our inventory levels up and continued to order.”
Used equipment pricing has gone sky high as inventory levels have dropped. “We’ve just had to get creative on how we go out and source equipment, acquiring lease returns, actively purchasing machines on the open market and using consignment programs,” Brian says.
Some pandemic-prompted changes, such as curbside parts pickup, are here to stay, says Lauren. “We had just launched our online parts portal before the pandemic, so it was easy to transition customers over to that tool.” Curbside parts pickups are now in front of all West Side branches.
The pandemic also exacerbated an already shallow talent pool, especially for ever-elusive technicians. In addition to reaching out with social media and forming relationships with tech schools, West Side is focusing on retention by using a new orientation for incoming employees. “The hardest time to keep them is when they’re new,” Diane says. “We want to make sure that they immediately feel part of the team.”
West Side’s employee culture program, Gear Up, has been in place since 2015. “We launched it with the goal of being the number one customer service provider in our industry,” Lauren says.
“We want to create ‘wow’ customer experiences throughout all of our departments. It really had us focus on our core values and creating this content that we now use for recruiting. We’re in a good place now because we have a lot of those facets that were already built out.”
Rokbak Sales Start Strong in North America
The first Rokbak units have reached U.S. shores and dealers are snapping them up, the company says.
The articulated hauler manufacturer, formerly known as Terex Trucks, has received confirmed orders from almost all dealers across the U.S., including:
Bane Machinery, B-C Equipment Sales and Easton Sales & Rentals in Texas >G.W. Van Keppel, with locations across the Midwest >Hills Machinery, Carolinas>Border Equipment, Georgia >Lawrence Equipment, Virginia>
Under the Rokbak brand, Volvo Group subsidiary Volvo Construction Equipment is offering two models, the 30.9-ton RA30 and the 41.9-ton RA40. The units offer fuel economy, lower emissions, improved safety, and greater durability than previous Terex Truck TA300 and TA400 models.
“We knew once we launched as Rokbak that the response would be positive because we have such a strong relationship with our dealers,” says Robert Franklin, director of sales – Americas at Rokbak. “But even we were surprised by just how successful our new direction has been. We’ve got a long history in the U.S. and Canada in our previous incarnation, but it’s exciting to see how enthusiastic our partners are about our new direction and backing up that enthusiasm with multiple orders.”
Rokbak offers two models: the 30.9 US ton payload RA30 and 41.9 US ton payload RA40.RokbakRokbak says orders are a mix of RA30 and RA40 units, with some already confirmed for delivery to end user customers, while others will join dealers’ rental or sales stock.
“Although the Rokbak brand has only existed a couple of months, it’s evolved from one of the world’s oldest hauler manufacturers,” says Kyle Fuglesten, COO at Hills Machinery. “We’ve been really impressed by the new branding – there is absolutely no doubt what it stands for. The team’s commitment to hard work, reliability, performance and environmental care are front and center – and with the Volvo Group’s backing, the quality is 100% guaranteed.”
Easton Sales and Rental took delivery of the first-ever Rokbak articulated hauler in early November. The RA30 was immediately sold to Linco Construction in Houston.
“Our business is built on delivering quality work that is competitively priced and performed by experts, so these new Rokak machines are ideal tools to help us do that,” says Steve Brown, president of Linco Construction. “They’ve only been at work for a few weeks, but we can already see they are workhorses. We have built relationships with our clients on our commitment, hard work and quality, and when we look at the Rokbak haulers, we see those same values shining through.”
Dozens more of the eye-catching grey haulers are set to arrive in North America in the coming months.
“We are so thankful for the loyalty and support of our customers and dealers in the U.S. and worldwide,” said Paul Douglas, managing director of Rokbak. “We are excited to demonstrate our passion, personality and skill under our new brand and can’t wait to see the first units at work on project sites.”
Did you miss our previous article…
https://constructionosa.org/?p=1034